DALLAS — There was once a time when the echoing sounds of rivets hammered into aluminum hulls set the pulse of the aerospace industry: enormous automated machines, intricate assembly templates, and warehouses filled with spare components defined the norm.
Aircraft were forged with passion yet restricted by the limitations of conventional manufacturing methods. The process was plodding, inflexible, and expensive. Still, it propelled us toward the jet era, to setting foot on the moon, and eventually to modern global air travel.
Yet brewing quietly in the background was a revolution. What started as a tool for experimenting with layering resin to mold simple forms has since evolved into a disruptive power redefining how we conceptualize, fabricate, and support aircraft. This power is additive manufacturing, also known as 3D printing.
No longer confined to research labs and pioneers, additive manufacturing now competes with traditional techniques on the factory floors of Boeing, Airbus, and NASA’s space missions.
This post outlines how necessity and innovation drove the aerospace sector to embrace 3D printing not merely as a novelty but as a strategic enabler of sustainability, efficiency, and the future of flight.
When Metal Met Laser: From Dream to Deployment
Aviation demands both precision and performance. Engineers have always sought to exceed the limits of what materials and equipment could accomplish. Nonetheless, conventional production had its constraints, particularly when dealing with complex geometries, internal cooling channels, or parts that needed to be both strong and lightweight.
That’s where additive manufacturing changed the game. Creating things, layer by layer, typically made of titanium or high-performance polymers like PEEK and PEKK, as well as nickel-based alloys, 3D printing broke free from the constraints of traditional production.
A pivotal moment occurred in 2016 when GE Aviation brought out its 3D-printed fuel nozzle for the LEAP engine. What might once have been manufactured by constructing it from 20 individual parts was now a single piece that weighed 25% less and had a life expectancy five times longer. It wasn't just a dare, but what lay ahead for additive manufacturing was bright.
When the Airbus A350 XWB program was launched, a similar exchange occurred. In each aircraft, it now contains over 1000 3D-printed parts, ranging from cabin brackets to ventilation ducts. These components reduced weight, made installation easier, and showed that production-level additive manufacturing was not a fantasy but a reality.
Weight, Waste, Winning Margins
In aviation, weight is everything. Each kilogram you can shave off an airframe or engine means better fuel economy, more extended range, and reduced emissions. Typically, manufacturers machined parts from solid blocks of titanium or steel, cutting away most of the material. It was effective but wasteful. Additive manufacturing turned that on its head.
- Weight reduction: Leads to fuel savings, increased range, and higher payload capacity.
- Complex geometries: Allow for enhanced aerodynamics, better heat management, and improved performance.
- Part consolidation: Results in fewer joints, less maintenance, and reduced failure points.
On-demand production: Helps reduce inventory needs and minimizes Aircraft on Ground (AOG) risk. - Customization: Enables mission-specific parts and improves the passenger experience.
- Less material waste: Supports sustainability goals and lowers raw material costs.
3D-printed lattice structures, which are typically unfeasible with traditional fabrication, are now being used to strengthen interiors while cutting weight. In one case, Lockheed Martin printed in titanium satellite antenna supports destined for NASA's Mars missions, thereby reducing mass and launch costs by tens of thousands of USD per kilogram.
The New Material World
Without innovation in materials, none of this would have been possible. The extremes of temperature and corrosion that aviation can experience require high-performance materials; they also have severe effects on fatigue.
The table below summarizes the most commonly used materials in aerospace additive manufacturing:
- Titanium alloys (e.g., Ti-6Al-4V): Used in engine parts and brackets. Offers high strength-to-weight ratio and excellent corrosion resistance.
- PEEK / ULTEM: Applied in interior panels and wire harness covers. Known for being flame-retardant, lightweight, and mechanically stable.
- Inconel (Nickel alloys): Used in turbine blades and exhaust components. Withstands temperatures over 700°C and remains strong under high stress.
- Carbon fiber composites: Common in UAV bodies and aerodynamic fairings. Noted for high stiffness, directional strength, and ultra-lightweight properties.
- Aluminum alloys: Utilized in non-critical airframe structures. Machinable, cost-effective, and lightweight.
These sophisticated fabrics are typically matched with compound 3D printers and follow-up procedures such as warm isostatic pressing or surface treatment to meet airworthiness standards.

Challenges in the Layer-by-Layer World
Additive manufacturing has hit some bumps in the road of aviation, despite its great potential.
The core concern is quality assurance. And compared to traditional processes like casting or forging, 3D printing's layer-by-layer approach introduces a new set of defects. These can be as serious as microcracks or tiny voids (or gaps), or uneven material properties across layers, all of which pose risks that need to be considered in safety-critical components.
To combat this, aerospace OEMs have resorted to nondestructive testing techniques such as CT scanning and ultrasonic inspection. In-situ monitoring is yet another confidence-building measure: lasers, cameras, and sensors track real-time build parameters.
Certification is a hurdle, too. The FAA and EASA are still formulating parameters for additive processes. In 2017, Boeing's 787 ECS duct became the first polymer part to be certified for commercial aviation—a milestone, but not the goal.
The industry is working together through ASTM's F42 to establish standards for the qualification of materials and equipment. Airbus, in particular, has taken the lead in defining digital threads, data perfectibility, and simulative validation.
From Hangar to Orbit: Expanding the Horizon
What began with cabin brackets and fuel nozzles has morphed into complete structural integration and even space missions.
The first 3D printer to ever be tested in space was aboard the International Space Station in 2014, a collaboration between NASA and Made In Space. By 2021, astronauts were manufacturing tools and spare parts on demand, in microgravity, and on the same space station, sidestepping expensive resupply launches. The long-term goal is to produce habitats and components on Mars using local materials and 3D printing robots.
On Earth, Lufthansa Technik’s in-house additive hubs now churn out custom seatbelt holders and tray tables. The outcome is reduced logistics holdups, improved part availability, and customized cabin designs.
On the other hand, Airbus has tested topology optimization and generative design algorithms that mimic the structure of bones to create parts that are stronger, lighter, and designed for organic shapes. But these designs, only capable of being made through additive methods, are stretching the limits of what an aircraft can be.
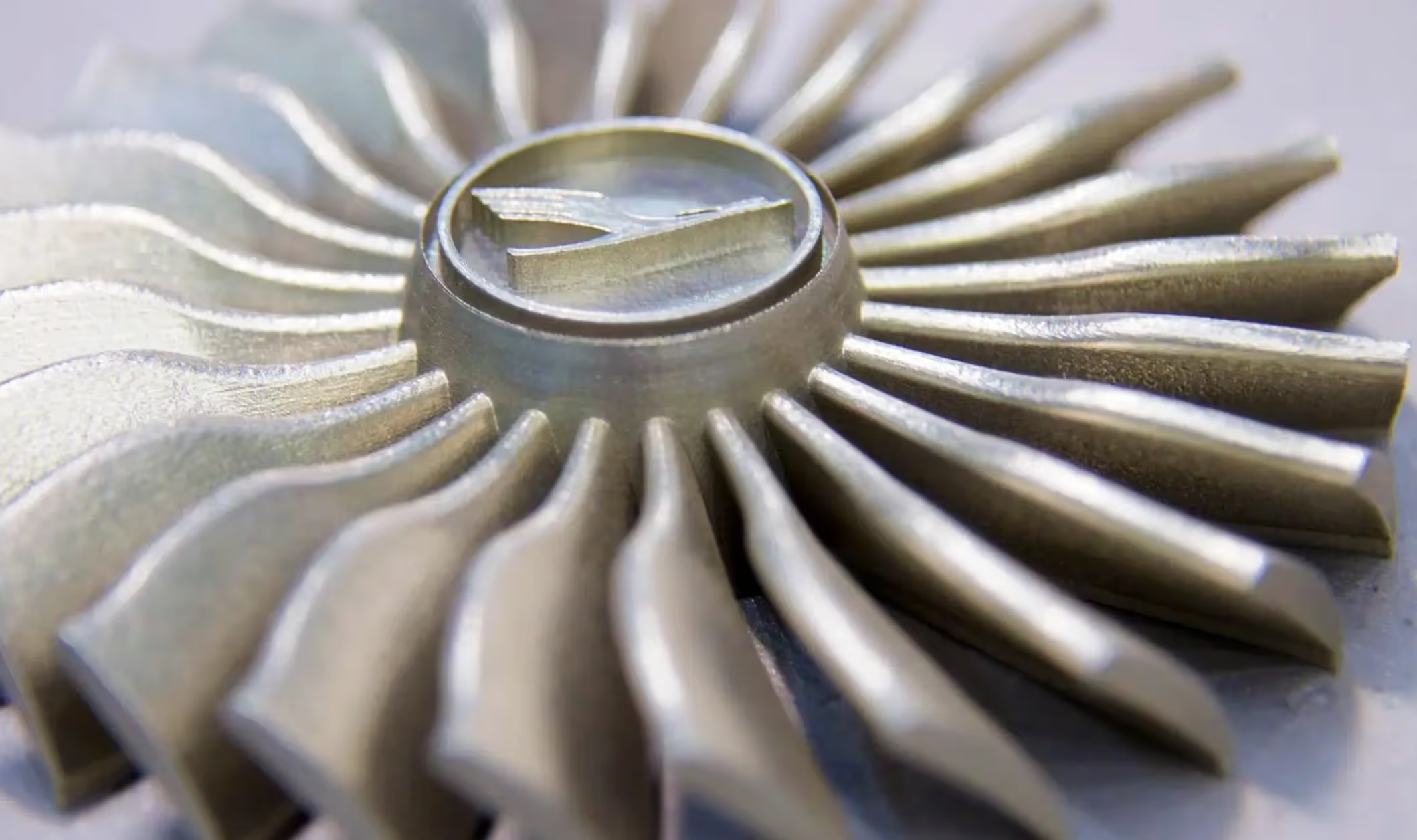
The Green Shift: Toward Sustainable Aviation
Aviation is under pressure to decarbonize. While electric propulsion and Sustainable Aviation Fuels (SAFs) make headlines, manufacturing is also contributing to reducing aviation’s environmental footprint.
Additive manufacturing is impactful in two significant ways:
- Material Efficiency: Traditional methods lose 90% of the material. 3D printing uses only what is required, reducing waste.
- Lightweight Design: The lighter the aircraft, the less fuel it consumes. According to Airbus, each kilogram saved translates into an estimated fuel savings of $ 3,000 over 25,000 flight hours.
Because of this, metal additive manufacturing was able to reduce the amount of material used in one study by a significant amount; about 60% less material was used with metal additive manufacturing than with traditional machining, while energy consumption decreased by about 30%. For an industry operating on thin margins and under scrutiny for its climate impact, these figures are significant.
Looking Ahead: What’s Next for Aerospace 3D Printing?
The field of additive manufacturing in aviation is currently at an inflection point. Emerging trends include:
- Multi-material printing: For parts that need various types of conductive, thermal, or mechanical properties.
- AI-based Manufacturing: For defect prediction, print parameters optimization, and self-sufficient production.
- Digital twins: These virtual representations of physical parts simulate stress, wear, and performance before printing even begins.
- Spare parts on demand: Airlines print parts in maintenance bases to decrease Aircraft on Ground (AOG) time.
Already, companies are blending additive with subtractive techniques, in which rough shapes are printed and then machined to tolerance. With hybrid manufacturing, speed and accuracy come together, as wearable 3D printing becomes feasible on a large production scale. Additive manufacturing is no longer just the future; it’s on the factory floor due to increasing use cases and a maturing ecosystem.
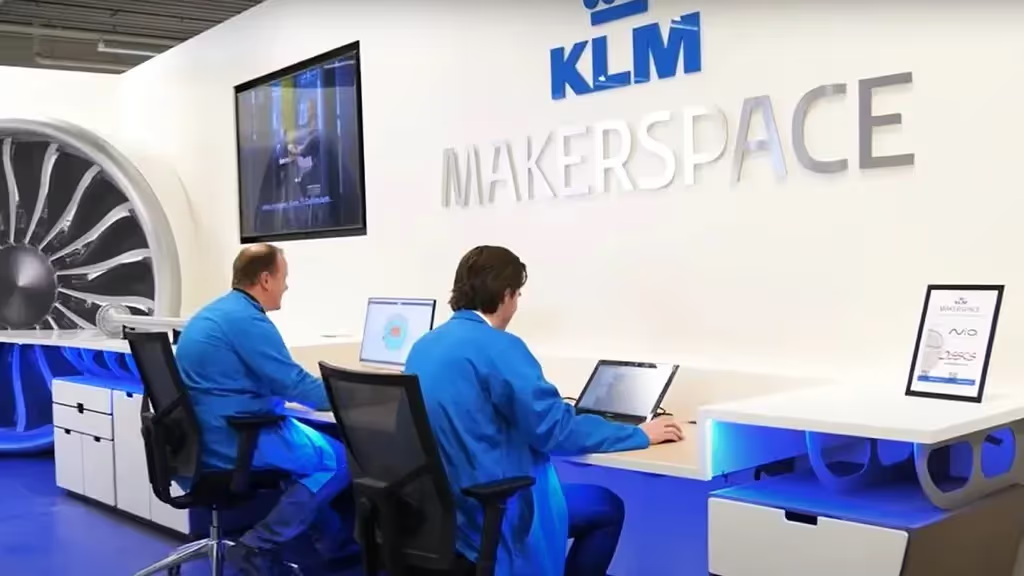
Conclusion: From Craftsmanship to Code
Aircraft used to be handcrafted, artistry tempered by plans and expertise. Today, we are entering an age where aircraft are born of algorithms, imitated in software, and printed into being.
Additive manufacturing has not displaced traditional aviation engineering; it has enhanced it. It’s more than a tool—it’s a philosophy: build smarter, lighter, and faster. From G.E.’s fuel nozzles to Airbus’s cabin fittings, from orbiting toolkits to A.I.-optimized wings, the industry is part of a new mode of thinking.
As sustainability pressures rise, innovation accelerates, and supply chains evolve, 3D printing will continue to play a defining role in aviation’s next great leap. Because in aviation, the best way to stay ahead is to build the future, one layer at a time.
Stay connected at every stop along your journey! Get any Saily mobile data plan at 5% off with the code AIRWAYSMAG5 + up to 5GB free!
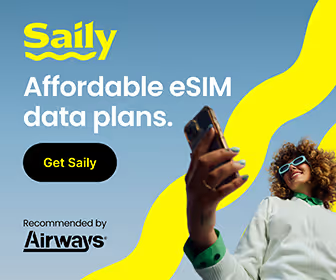