DALLAS — Aircraft engine maintenance has traditionally been time-consuming and costly, requiring extensive downtime and meticulous inspection procedures to ensure flight safety.
The emergence of nanobot and microbot technologies promise to transform how aircraft engines are inspected and maintained. These miniature robotic systems, developed by major aerospace companies like GE Aerospace and Rolls-Royce, can navigate the complex internal structures of jet engines to detect defects, corrosion, and other issues that might compromise performance or safety.
By enabling faster, more thorough inspections without requiring engine removal, these technologies have the potential to reduce maintenance costs, minimize aircraft downtime, and enhance aviation safety through early detection of potential problems.
The Evolution of Aircraft Engine Inspection Technology
Aviation maintenance has historically relied on manual inspection techniques that necessitate substantial engine disassembly, resulting in extended aircraft grounding and high labor costs.
The introduction of borescope technology represented an initial step toward less invasive inspection methods, but this approach still has significant limitations. Borescopes can be challenging to maneuver in complex engine geometries, and their effectiveness is often limited by factors such as gravity, which can cause the borescope's tip to settle naturally when not braced against a structure within the engine.
Additionally, traditional inspection methods may miss microscopic defects that can later develop into serious issues, potentially compromising aviation safety. These limitations have driven aerospace manufacturers to explore innovative solutions that provide more comprehensive, efficient, and less invasive inspection capabilities.
The development of robotic inspection systems has progressed rapidly over the past decade, with significant advancements occurring between 2018 and 2025. This evolution has been driven by collaborations between significant aerospace companies and leading research institutions, resulting in diverse robotic inspection technologies.
These systems leverage materials science, robotics, artificial intelligence, and miniaturization advances to create sophisticated tools capable of navigating the challenging environment inside aircraft engines. The progression from tethered, operator-controlled devices to increasingly autonomous systems represents a fundamental shift in how engine inspections are performed, promising to enhance the efficiency and effectiveness of maintenance procedures across the aviation industry.
Current Nanobot Technologies in Development
GE's Sensiworm Technology
GE Aerospace has developed a groundbreaking robotic platform called Sensiworm (Soft ElectroNics Skin-Innervated Robotic Worm), representing a significant advancement in engine inspection technology. Unveiled in 2023, this innovative robot draws inspiration from inchworms, utilizing untethered soft robotics technology to move quickly through the intricate internal structures of jet engines.
The Sensiworm's flexible body enables it to navigate through narrow passages and around curved surfaces inaccessible to more rigid inspection tools. This biological-inspired design reflects a growing trend in robotics toward soft, compliant structures that can safely interact with delicate or complex environments without causing damage. The development of Sensiworm involved collaboration between GE Aerospace, SEMI Flex Tech, Binghamton University, and UES, Inc., demonstrating the interdisciplinary approach required to create these sophisticated inspection systems.
The Sensiworm has several advanced capabilities that make it well-suited for engine inspection tasks. It is equipped with sensors that can detect defects and corrosion while measuring the thickness of an engine's thermal barrier coatings, providing valuable data about component conditions and potential maintenance requirements.
The robot employs a sticky, suction-like bottom surface that enables it to climb and adhere to steep or even inverted surfaces within the engine, overcoming the gravity limitations restricting conventional inspection tools. An operator uses a device similar to a gaming controller to manage the Sensiworm, and the robot can be programmed to follow specific inspection paths for consistent coverage.
This combination of flexible movement, advanced sensing capabilities, and intuitive control makes the Sensiworm a powerful tool for performing comprehensive engine inspections without requiring disassembly.
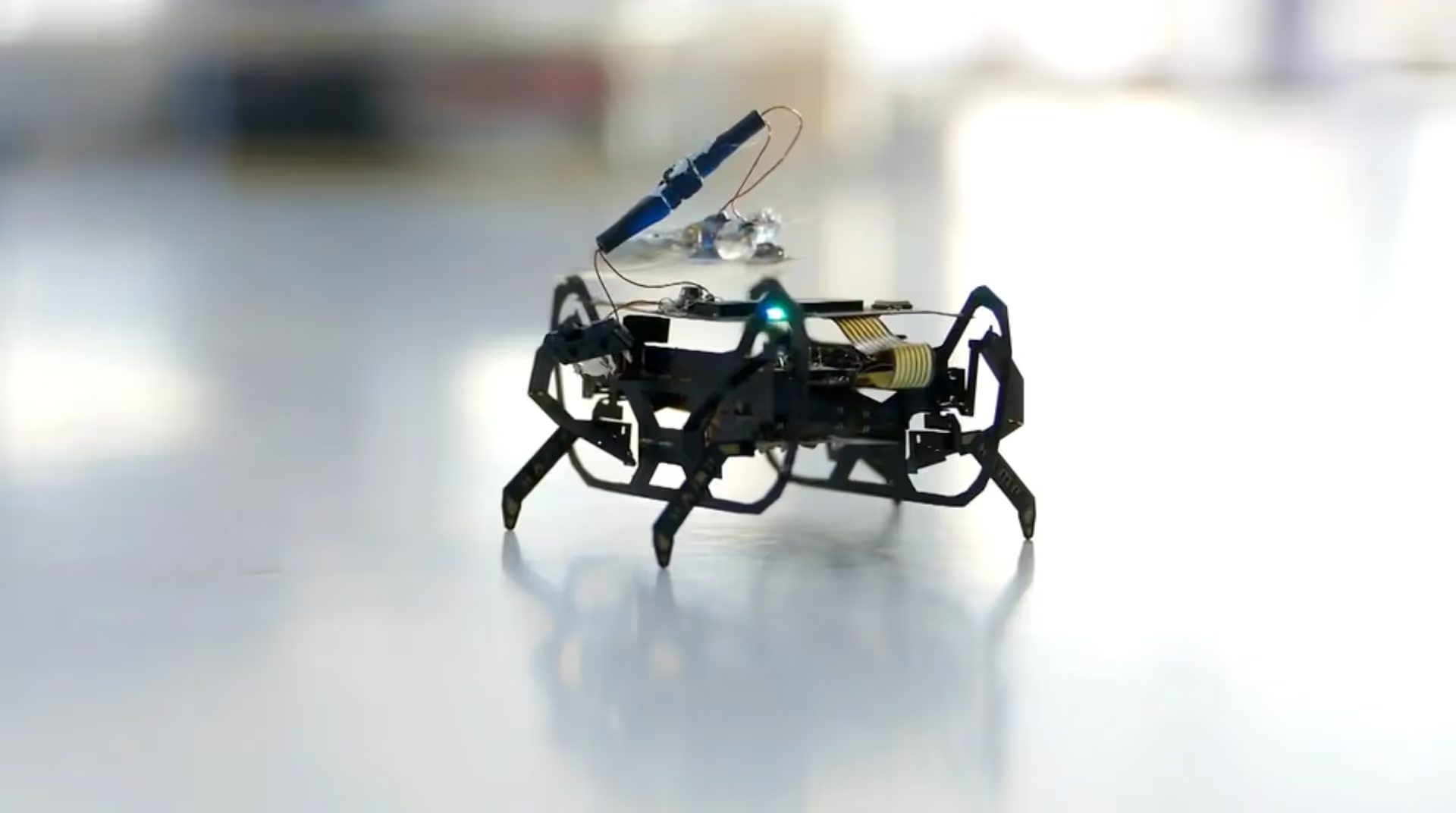
Rolls-Royce's SWARM Robots
Already in 2018, Rolls-Royce was taking a different approach to engine inspection by developing SWARM robots in collaboration with the University of Nottingham and Harvard University. These microbots, each approximately 10mm in diameter, are designed to be deposited into the center of an engine via a larger 'snake' robot. Afterward, they can crawl around to conduct visual inspections of hard-to-reach areas.
Each microbot has a tiny camera that provides live feedback to human operators, enabling real-time visual inspection of engine components without disassembly. According to Rolls-Royce technology specialist James Kell, these robots could dramatically reduce inspection times from approximately five hours using conventional methods to potentially just five minutes, representing a significant improvement in maintenance efficiency. This substantial time saving directly reduces aircraft downtime and operational costs for airlines and operators.
The development of SWARM robots at Rolls-Royce demonstrates the company's commitment to innovation in maintenance technology. The company has already developed microbots measuring 4.5 cm in length and is making progress on further miniaturization to enhance their capabilities.
In addition to the SWARM robots, Rolls-Royce is developing "Inspect" robots, approximately the size of a pencil, which would be permanently embedded within the engine. Protected by thermal shielding, these robots would enable the engine to inspect itself continuously, providing real-time monitoring of engine conditions. This multi-tiered approach to robotic inspection, encompassing both deployable microbots and permanently installed monitoring systems, illustrates the comprehensive strategy that Rolls-Royce is pursuing to transform engine maintenance practices.
These technologies form part of the company's IntelligentEngine vision, in which products and services become so closely connected that they are inseparable, enabling more proactive and responsive maintenance approaches.
Complementary Inspection Technologies
In addition to the specialized nanobots and microbots being developed for internal engine inspection, broader robotic platforms are emerging to address external aircraft inspection needs.
The CompInnova project, funded by the EU's H2020 Framework Programme and coordinated by Cranfield University, has developed a four-wheel robot called the Vortex Robot that can move around the exterior surface of an aircraft. This robot uses intense suction to adhere to the aircraft surface and is equipped with ultrasonic sensors and infrared thermography to perform structural inspections.
Implementing such technologies demonstrates how robotic inspection systems are being developed for various aspects of aircraft maintenance, not limited solely to engine components. This holistic approach to inspection robotics suggests a future where specialized robots might work together to provide comprehensive aircraft maintenance coverage.
The concept of highly miniaturized inspection devices extends beyond current implementations to theoretical proposals like the NanoJet. This concept envisions insect-sized devices with cameras and sensors that rapidly access difficult-to-reach areas and transmit visual and sensor data to maintenance personnel.
While such extreme miniaturization presents significant technical challenges, it illustrates the potential long-term evolution of inspection robotics toward increasingly smaller and more specialized devices. As nanotechnology continues to advance, the capabilities of these microscopic inspection systems will likely expand, enabling even more comprehensive and non-invasive maintenance approaches.
The progression from current microbot technologies to actual nanoscale devices represents an exciting frontier in aviation maintenance innovation.
Operational Mechanisms and Advanced Features
Movement, Navigation Systems
The effectiveness of engine inspection robots depends significantly on their ability to navigate the complex internal geometry of jet engines, requiring sophisticated movement mechanisms tailored to their specific design and purpose. GE's Sensiworm moves like an inchworm and utilizes a suction-based system to adhere to surfaces, allowing it to climb steep or inverted sections of engine components without falling.
This biomimetic approach to locomotion enables the robot to overcome the limitations of gravity that restrict conventional inspection tools, providing access to areas that would otherwise require substantial disassembly to inspect. The Sensiworm's soft, compliant construction ensures it won't damage sensitive engine components during inspection, addressing a critical concern for maintenance procedures.
This combination of flexible movement and secure adhesion represents a significant advancement in robotic locomotion designed for the challenging environment inside aircraft engines.
Rolls-Royce's SWARM robots employ different movement mechanisms appropriate to their smaller size and specific inspection tasks. These microbots are designed to crawl through engine compartments after being deployed by larger snake-like robots that deliver them to the engine core. The snake robots feature articulated segments that can bend and twist to navigate through narrow passages within the engine, allowing them to reach areas inaccessible to larger devices.
Meanwhile, the Vortex Robot developed under the CompInnova project uses motorized wheels and force sensors that measure adhesion around an aircraft's exterior surface. These diverse robotic movement and navigation approaches highlight how different mechanisms are being developed to address the specific challenges associated with various inspection environments, from engine interiors to aircraft exteriors.
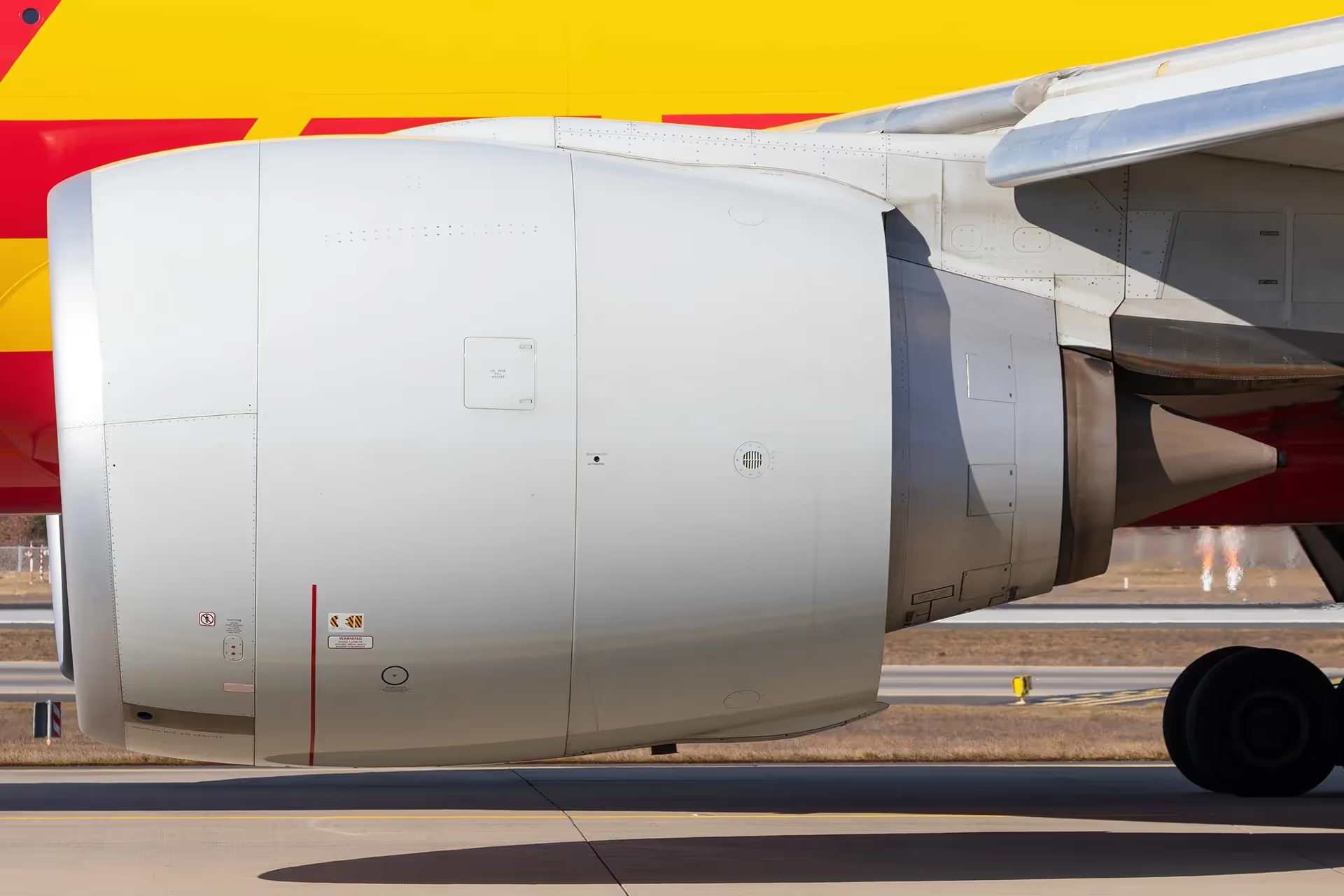
Sensing, Inspection Capabilities
Modern inspection robots incorporate a variety of sensors and imaging technologies that enable them to detect issues that might be invisible to human inspectors. Most systems feature cameras that provide live video feeds to operators, allowing for detailed visual inspection of components without requiring disassembly.
GE's Sensiworm goes beyond visual inspection by incorporating sensors that can detect defects and corrosion while measuring the thickness of thermal barrier coatings, providing valuable quantitative data about component conditions. This multi-modal sensing approach enables a more comprehensive assessment of engine health than would be possible with visual inspection alone.
The ability to measure coating thickness is particularly valuable since thermal barrier coatings play a critical role in protecting engine components from extreme temperatures, and their degradation can significantly impact engine performance and lifespan.
More advanced inspection systems integrate sophisticated sensing technologies to provide more detailed component analysis. The Vortex Robot developed through the CompInnova project incorporates ultrasonic sensors for in-depth characterization of damage types and infrared thermography for broader initial assessments.
This complementary use of different sensing modalities enables a hierarchical inspection approach, where thermography provides a rapid overview to identify potential problem areas, and ultrasonic inspection follows to characterize specific issues in greater detail. According to research on emerging nanobot technologies, these systems can perform real-time inspections capable of detecting microscopic cracks and corrosion in airplane components that would be invisible to the naked eye.
This enhanced detection capability represents a significant advancement in maintenance technology. It allows issues to be identified and addressed before they develop into more serious problems that could compromise safety or performance.
Communication, Control Systems
Effective communication between inspection robots and human operators is essential for maximizing the utility of these advanced technologies. Most current systems wirelessly transmit video and sensor data to control stations where technicians can analyze the information and direct further inspection activities.
Control interfaces range from devices similar to gaming controllers for GE's Sensiworm to more sophisticated systems that can program specific inspection paths and protocols. As these technologies mature, the trend is moving toward increased autonomy, with robots capable of following predetermined routes through engines without continuous human guidance.
This evolution toward semi-autonomous operation promises to enhance inspection consistency while reducing the demands on human operators. Technicians will be able to supervise multiple inspection robots simultaneously.
The integration of artificial intelligence represents a significant advancement in processing and analyzing the vast amounts of data generated during robotic inspections. GE Aerospace has been incorporating AI into its inspection tools to help technicians identify which images to review, ensuring greater consistency in spotting potential issues while reducing inspection times by approximately 50%.
This AI-enabled approach has been deployed across over a dozen GE Aerospace MRO facilities and to customers servicing the CFM LEAP engine, demonstrating its practical utility in real-world maintenance environments. Combining robotic inspection platforms with AI-powered analysis tools creates a powerful synergy that enhances the efficiency and effectiveness of maintenance procedures.
As AI capabilities advance, we can expect further improvements in defect detection accuracy and inspection speed, ultimately contributing to safer and more reliable aircraft operations.
Benefits, Impact on Aviation Maintenance
Efficiency, Cost Advantages
One of the most significant advantages of robotic inspection systems is their potential to reduce the time required for engine inspections dramatically. According to Rolls-Royce representatives, traditional methods might need five hours to complete certain inspections, while robot-assisted approaches could reduce this to just five minutes.
This efficiency improvement translates directly into reduced aircraft downtime and lower operational costs for airlines and maintenance providers. GE Aerospace reports that its AI-enabled blade inspection tool has demonstrated a 50% reduction in inspection times compared to traditional methods, providing substantial time savings even with current implementations.
These efficiencies are particularly valuable in the commercial aviation sector, where aircraft on the ground represent significant revenue loss, and maintenance schedules must be carefully managed to minimize disruption to flight operations.
The economic impact of faster inspections extends beyond direct maintenance costs to encompass broader operational benefits. Aircraft maintenance typically accounts for about 20% of total operating costs, so any significant reduction in maintenance time and complexity can substantially impact an airline's financial performance.
By enabling on-wing inspections that don't require engine removal, robotic inspection systems minimize the labor costs associated with engine disassembly and reassembly while reducing the potential for handling damage during these procedures.
Furthermore, more efficient inspections allow for more flexible maintenance scheduling, enabling operators to better align maintenance activities with natural gaps in flight schedules. This optimization of maintenance timing can help airlines maximize aircraft utilization rates, further enhancing their operational efficiency and profitability.
Enhanced Safety Through Superior Detection
The advanced sensing capabilities of nanobots and inspection robots contribute significantly to aviation safety by enabling the detection of defects that might be missed during traditional inspections. These robotic systems can perform real-time inspections to identify microscopic cracks and corrosion in airplane components that would be invisible to the naked eye.
Early detection of such issues allows maintenance teams to address potential problems before they develop into serious failures that could impact flight safety. The consistency of robotic inspections also helps eliminate variability in inspection quality resulting from human factors such as fatigue or distraction.
GE Aerospace's AI-enabled inspection tool has improved consistency for spotting potential issues compared to traditional borescope methods, highlighting how these technologies can enhance the reliability of the inspection process.
The significance of improved defect detection is reflected in the substantial investments in advanced inspection technologies. Over five years, GE Aerospace has invested over US$1 billion in its MRO (Maintenance, Repair, and Overhaul) shops, demonstrating its commitment to enhancing aviation safety through advanced maintenance technologies.
This investment encompasses developing robotic inspection systems and integrating artificial intelligence to analyze inspection data more effectively. The company has been incorporating AI into its operations for over a decade. It holds numerous AI patents within the aviation industry, with applications ranging from engine monitoring and part inspections to predictive maintenance insights.
This comprehensive approach to maintenance technology innovation illustrates how nanobots and AI-enhanced inspection systems represent a broader transformation in ensuring aircraft safety through more effective and efficient maintenance practices.
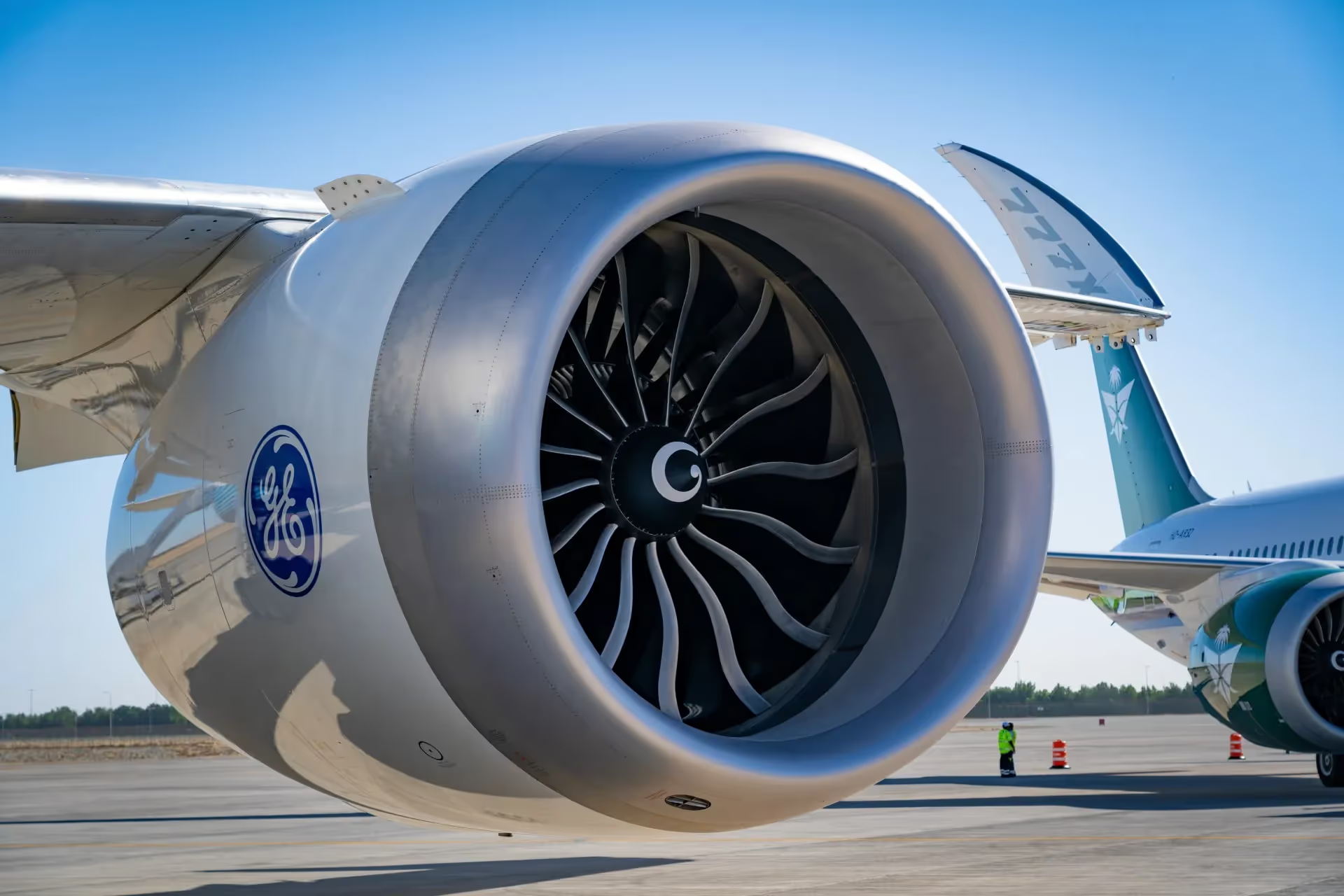
On-Wing Advantages, Minimizing Disruption
The most transformative aspect of robotic inspection technology is the ability to conduct thorough examinations while engines remain mounted on aircraft wings. Traditional inspection approaches often require engines to be removed for comprehensive assessment, a time-consuming, labor-intensive process that creates opportunities for handling damage. Robotic inspection systems can be deployed through an engine's turbine inlet or exhaust or existing access ports, eliminating the need for disassembly in many cases.
GE's Sensiworm and Rolls-Royce's SWARM robots are specifically designed to navigate the internal structures of mounted engines, providing detailed visual and sensor data without requiring removal. This capability represents a paradigm shift in maintenance procedures, potentially eliminating one of the most disruptive aspects of engine inspection.
The ability to perform on-wing inspections is particularly valuable for operators with tight flight schedules or limited maintenance resources. Aircraft grounded for engine removal face extended periods of unavailability, often measured in days rather than hours, resulting in significant operational disruption and potential revenue loss. Robots like the Sensiworm enable service operators to have "multiple additional sets of eyes and ears to perform on-wing inspections," as noted by Deepak Trivedi, principal robotics engineer at GE Aerospace1.
These systems can inspect every inch of a jet engine while transmitting live video and real-time data about component conditions, providing comprehensive coverage without the disruption associated with engine removal. As these technologies mature and are widely adopted, we expect a fundamental shift in maintenance planning and execution, with more frequent but less invasive inspections becoming the norm for ensuring engine health and performance.
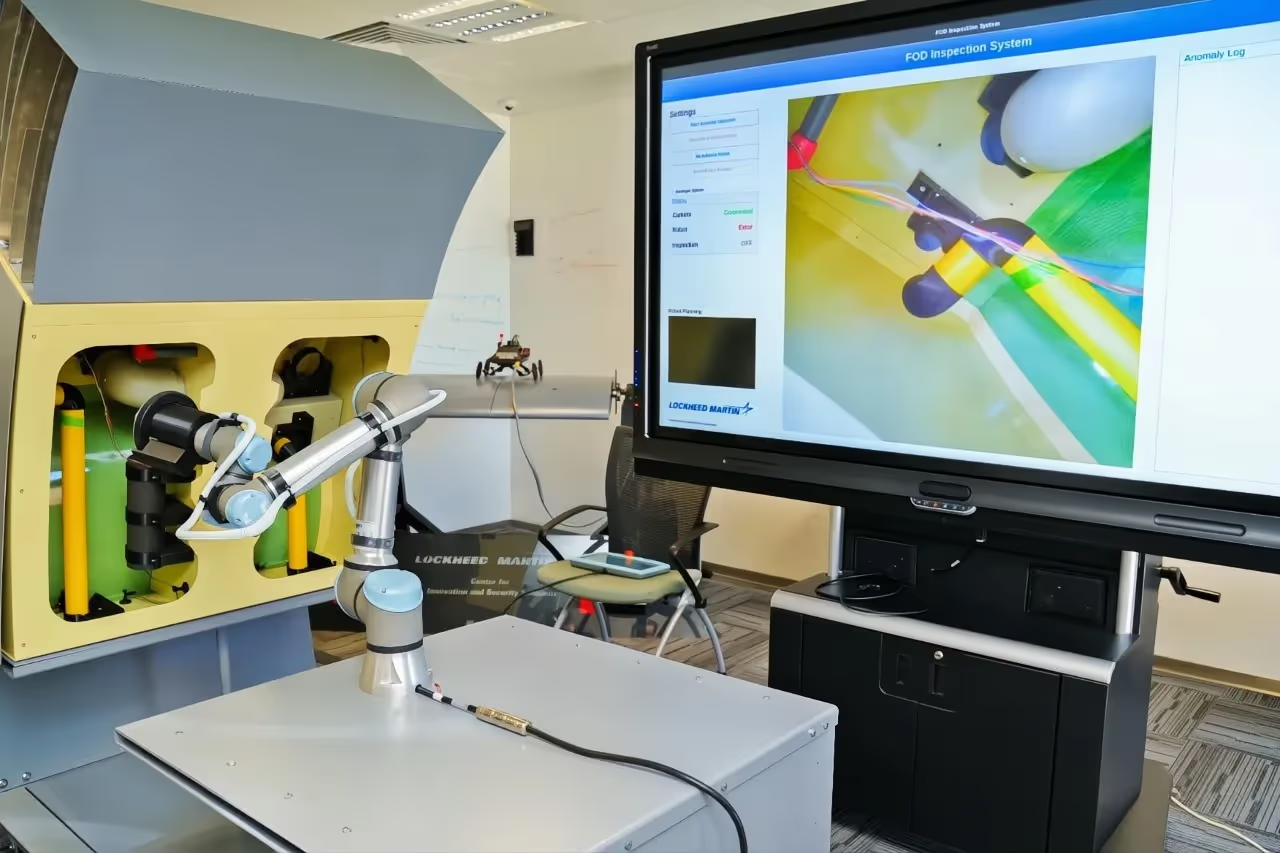
Implementation Challenges, Emerging Solutions
Technical Hurdles in Harsh Environments
Despite their promising capabilities, nanobots and microrobots for engine inspection face several significant technical challenges related to the harsh operating environment inside aircraft engines. Jet engines experience extreme temperatures, vibrations, and potential contamination that can disrupt robotic operations or damage sensitive components. Rolls-Royce's development of "Inspect" robots with thermal protection addresses some of these concerns by enabling continuous monitoring even under challenging conditions.
However, power supply remains a significant issue for untethered robots, limiting their operational time and the range they can cover during a single deployment. Similarly, communication within the metal confines of an engine can be problematic, potentially restricting the transmission of high-quality video and sensor data necessary for adequate inspections. These technical limitations require innovative solutions in materials science, power management, and communication technologies to ensure reliable performance under all operating conditions.
As these robotic systems become increasingly miniaturized, manufacturing challenges become more significant. Producing tiny components with the necessary precision, durability, and reliability requires advanced manufacturing techniques that may not be widely available. The NanoJet concept highlights how the scaling laws affecting Brayton cycle devices present unique challenges as size decreases, potentially involving factors such as the speed of sound, viscosity, and other physical properties that behave differently at microscopic scales.
Additionally, as robotic inspection systems transition from prototypes to widespread deployment, manufacturers must develop scalable production processes that meet industry demand while maintaining consistent quality and performance standards. The intersection of high-precision manufacturing requirements with the need for volume production represents a significant challenge that must be addressed to enable the broad adoption of these technologies across the aviation industry.
Integration with Maintenance Workflows
Incorporating robotic inspection systems into established maintenance workflows requires careful planning and adaptation to maximize their benefits while minimizing disruption. Maintenance technicians need comprehensive training to operate these new tools effectively, interpret the data they provide, and translate it into appropriate maintenance actions. GE Aerospace has been addressing this challenge by deploying its AI-enabled inspection tools across more than a dozen MRO facilities and to customers servicing the CFM LEAP engine, providing real-world experience with these advanced technologies.
This gradual implementation allows for the development of best practices and the refinement of integration strategies, ensuring that the transition to robotic-assisted maintenance proceeds smoothly. The company's approach demonstrates how introducing new inspection technologies must be accompanied by appropriate training and support to ensure effective utilization.
Regulatory considerations present another significant aspect of implementation that must be addressed. Aviation maintenance is heavily regulated to ensure safety, and certification authorities must develop appropriate standards and regulations for robotic inspection systems. These regulatory frameworks need to establish acceptable procedures for robotic inspections, define data validation and verification requirements, and outline training standards for technicians. GE Aerospace's emphasis on responsible AI use, with guidelines emphasizing human oversight, data integrity, and transparency, aligns with the regulatory expectations likely to emerge for these technologies.
As robotic inspection systems become more autonomous, regulatory approaches must evolve to address reliability, decision-making authority, and failure management questions. Developing appropriate regulatory frameworks is critical to successful implementation, ensuring these innovative technologies enhance rather than compromise aviation safety.
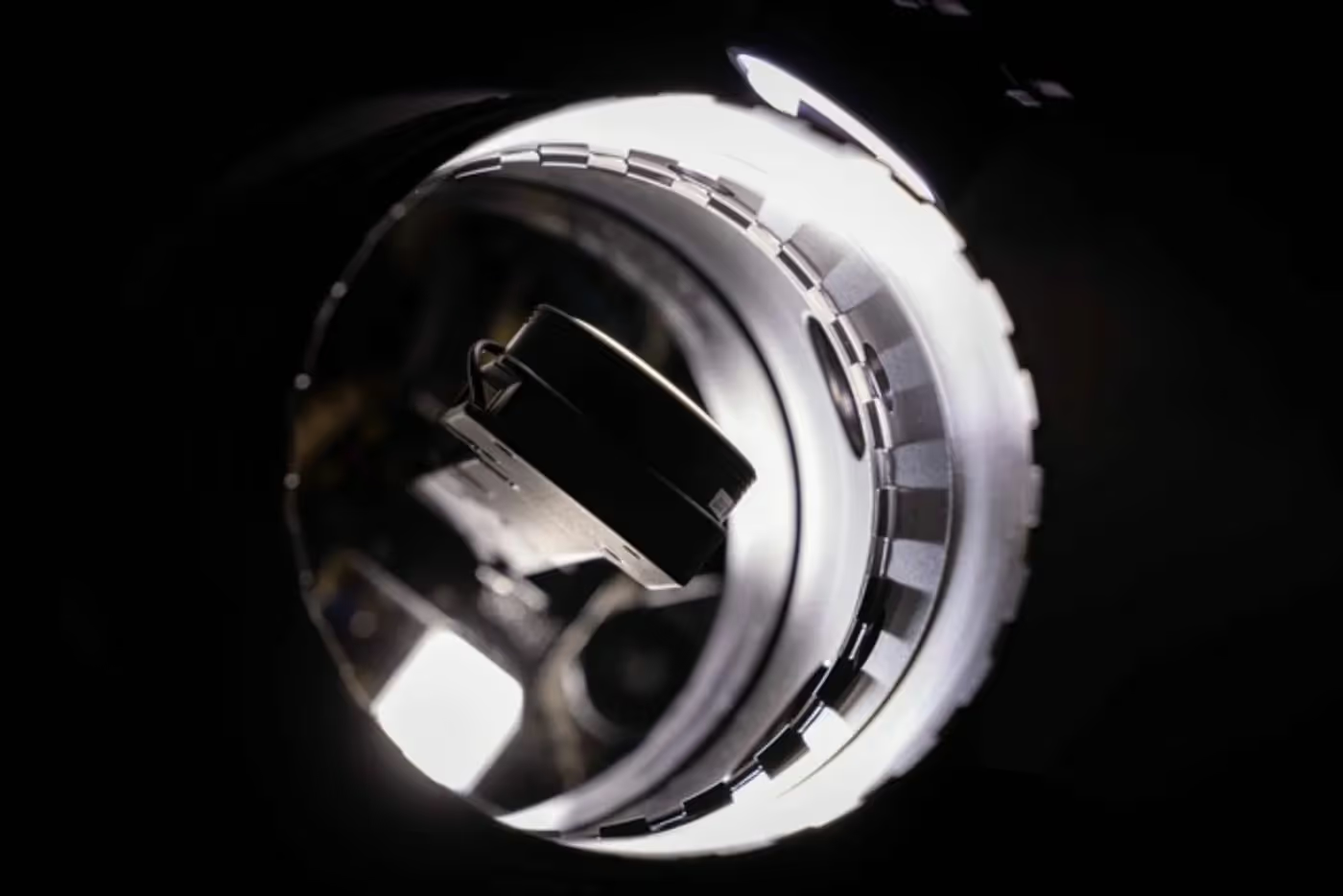
Future Trajectory, Emerging Trends
AI Integration, Autonomous Operation
The integration of artificial intelligence represents a major trend in the evolution of nanobot inspection technology, with significant implications for both current implementations and future developments. GE Aerospace's AI-enabled blade inspection tool, which helps technicians capture and analyze turbine blade images, demonstrates AI's potential to enhance the efficiency and accuracy of inspections. This technology has already shown significant improvements, reducing inspection times by approximately 50% while improving consistency in identifying potential issues.
The combination of robotic platforms for data collection with AI systems for analysis creates a powerful synergy that enhances both the speed and quality of maintenance procedures. As these AI capabilities advance, we expect increasing levels of automation in the inspection process, potentially allowing robots to identify and categorize defects with minimal human intervention.
The progression toward greater autonomy represents a natural evolution for robotic inspection systems. Current implementations typically require substantial human control and oversight, but future systems will likely incorporate more sophisticated autonomous navigation and decision-making capabilities.
This increased autonomy would allow inspection robots to follow predetermined routes through engines, adapting their paths to investigate potential issues they detect. More advanced systems might prioritize inspection areas based on historical data or predictive models, focusing on components with higher failure probabilities.
This evolution toward intelligent, semi-autonomous inspection platforms would further enhance maintenance efficiency while improving detection reliability through consistent, methodical inspection processes. However, this increased autonomy must be balanced with appropriate human oversight to ensure critical maintenance decisions remain subject to expert judgment and align with regulatory requirements.
From Inspection to Repair Capabilities
While current robotic systems primarily focus on inspection functions, future developments aim to equip these platforms with the ability to perform repairs. Rolls-Royce and its university partners are working to create robots that can complete maintenance tasks and repairs, going beyond simple inspection to address issues directly.
Similarly, emerging research suggests nanobots with autonomous repair capabilities could immediately address issues such as microscopic cracks upon detection, preventing them from developing into more significant problems. This evolution from passive inspection to active repair represents an important advancement that could further reduce maintenance times and costs while enhancing safety through prompt remediation of potential issues.
The development of repair capabilities would transform these robots from diagnostic tools to comprehensive maintenance platforms, fundamentally changing how engine servicing is performed.
The progression toward repair functionality presents substantial technical challenges that must be overcome. Miniaturized repair tools must be effective yet safe, addressing defects without risking damage to surrounding components. Repair procedures must be precisely controlled and validated to meet established airworthiness standards. Additionally, the regulatory framework for autonomous or semi-autonomous repairs requires careful development to develop appropriate boundaries and oversight mechanisms.
Despite these challenges, the potential benefits of in situ repair capabilities are substantial enough to drive continued research and development in this area. Successful implementation represents a revolutionary advancement in aviation maintenance, enabling continuous monitoring and repair that minimizes the need for scheduled downtime while maximizing component lifespan and performance reliability.
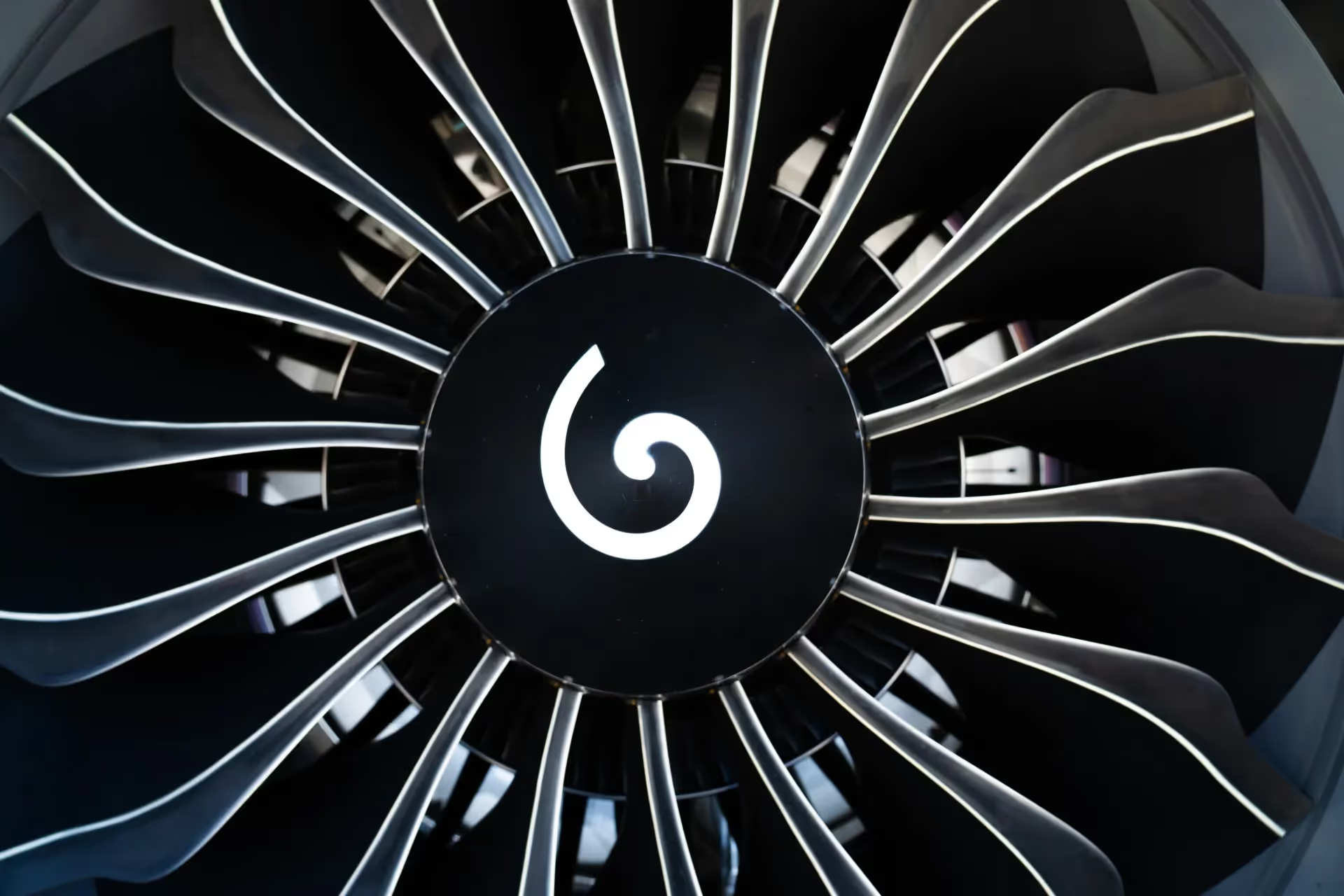
Industry Adoption, Future Outlook
The aviation industry's adoption of robotic inspection technology is gaining momentum, with major engine manufacturers like GE Aerospace and Rolls-Royce leading implementation efforts. GE's deployment of AI-enabled inspection tools across multiple MRO facilities indicates a commitment to integrating these technologies into standard maintenance practices.
The company has been using its AI-enabled blade inspection tool for three years on the GEnx wide-body aircraft engine, where it has demonstrated significant improvements in inspection speed and accuracy compared to traditional borescope methods.
This successful implementation provides valuable experience and validation, likely accelerating broader adoption across different engine types and maintenance facilities. As these technologies demonstrate their value through reduced inspection times, lower costs, and enhanced defect detection, we can expect accelerated industry-wide adoption that transforms standard maintenance practices.
The continued advancement of nanobot and microbot technologies promises increasingly sophisticated inspection and maintenance capabilities. Ongoing miniaturization efforts may eventually lead to true nanoscale devices capable of accessing previously unreachable areas of engines, providing even more comprehensive inspection coverage. Integrating advanced materials, improved power sources, and more sophisticated AI could enable longer-duration missions with enhanced sensing capabilities. Additionally, networks of specialized robots might work collaboratively to address various aspects of engine health, from visual inspection to material analysis and targeted repairs.
Stay connected at every stop along your journey! Get any Saily mobile data plan at 5% off with the code AIRWAYSMAG5 + up to 5GB free!
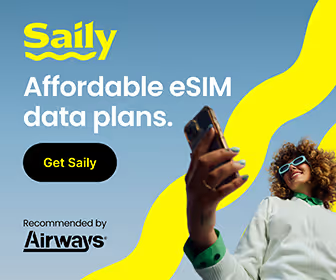