DALLAS — One of the essential components of any aircraft is the landing gear, which serves as the central support system during takeoff, landing, and ground movements.
The landing gear is key to maintaining an airplane's stability and controllability during ground movement, absorbing loads imposed by the landing or takeoff, and providing a smooth flight and ground movement transition. Poor-quality landing gear compromises safety and increases the risk of structural failure.
Over the decades, landing gear technology has evolved—from simple fixed designs on small aircraft to advanced, multi-bogie retractable systems—enhancing performance, safety, and efficiency.
Aircraft types, operational needs, and weight influences affect the design and arrangement of landing gears, from simple fixed ones on small general aviation planes to highly sophisticated multi-bogie retractable systems on large airliners.
A typical landing gear system includes structural members, hydraulics, energy-absorbing components, brakes, wheels, and tires. Steering devices and retracting mechanisms are other components that work together to facilitate smooth operations. These issues become critical in determining the aircraft's operational effectiveness, reliability, and maintenance costs.
Structural Members & Materials
The structural elements of the landing gear support any heavy landing loads and resist gear buckling from the aircraft's weight. These parts must be robust enough to hold the aircraft aloft during takeoff with a whole fuel load and withstand impact loads upon landing. Some of the materials that are usually used in landing gear are:
- High-strength steel – Offers excellent static strength and fatigue resistance.
- Titanium alloys (Ti-alloy) – Lighter, strong, corrosion resistant, and durable.
This is a good thing, but we don't want the impact forces on the pilot and passengers to be too high during a hard landing.
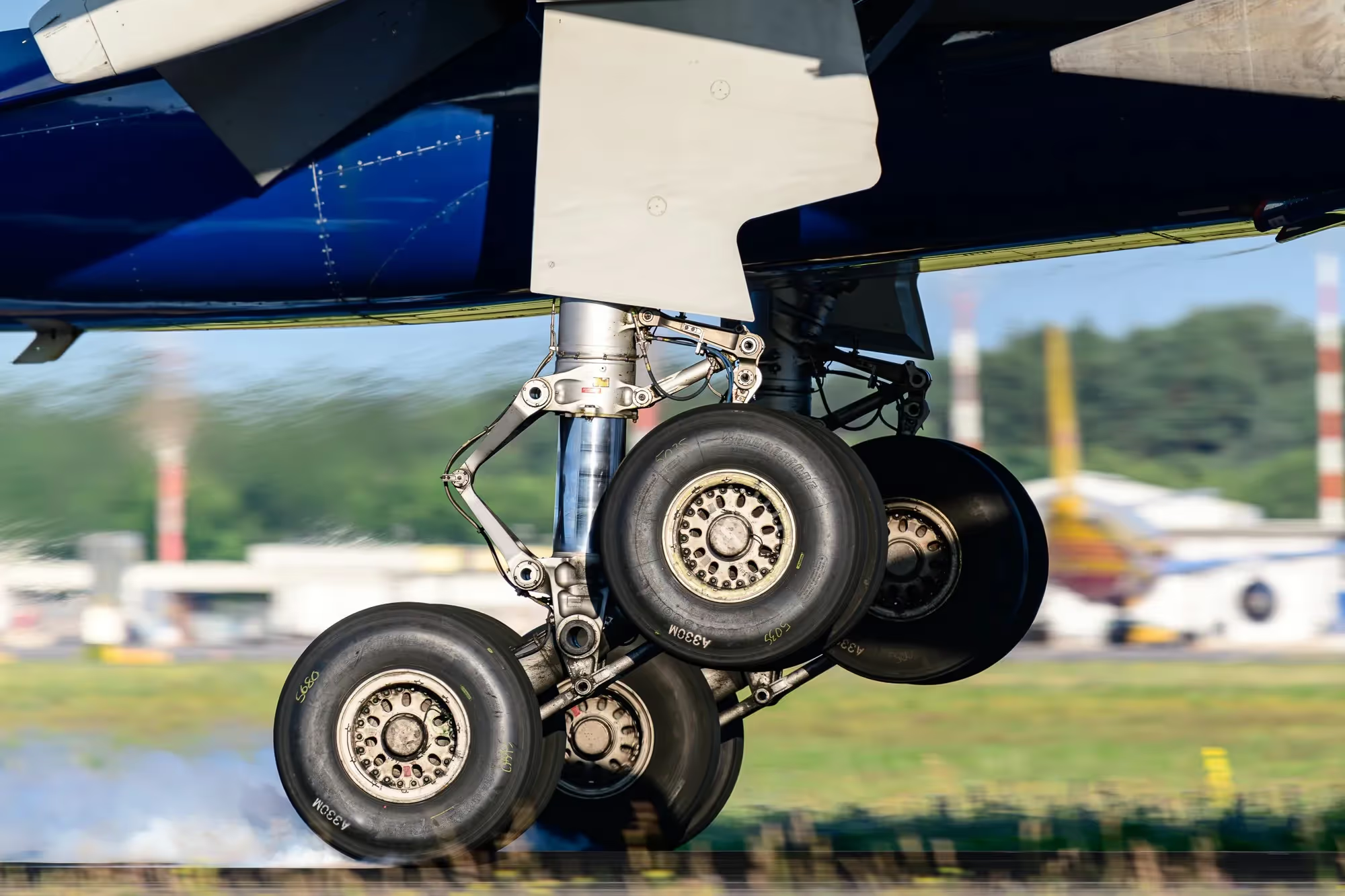
Considerations of Design and Function
While wheeled landing gear is most common, variations such as skis for snowy conditions, water floats, and helicopter skids cater to specific operational needs.
Retractable landing gears improve aerodynamics by reducing drag. Most aircraft have some variation of a 3-wheel or wheel-set configuration to ensure stability and balance.
The landing gear generally accounts for 2.5 to 5% of maximum takeoff weight (MTOW) and 1.5 to 1.75% of the aircraft's overall cost, while it contributes 20% of the airframe direct maintenance cost.
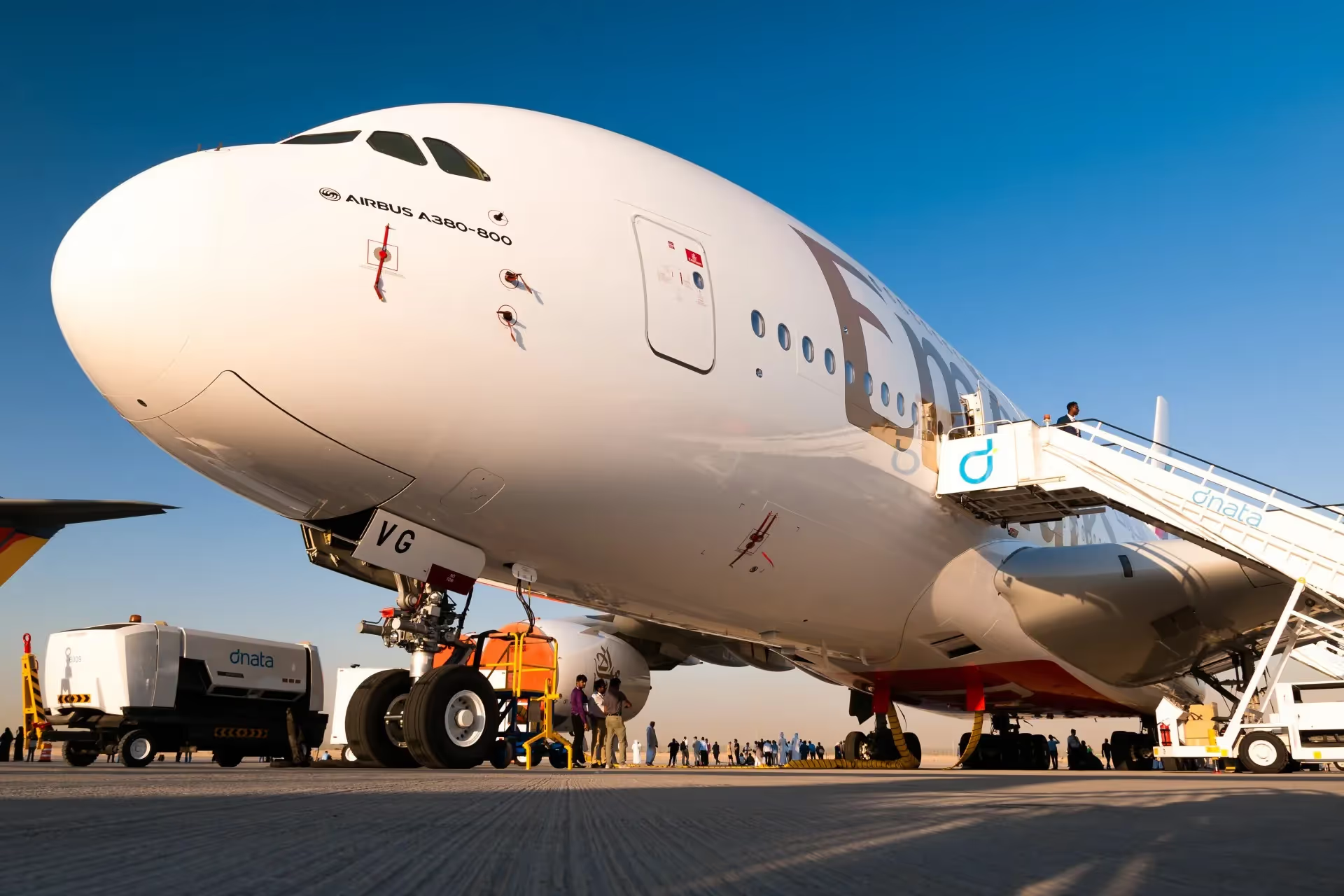
Retractable Gear
To reduce drag, the landing gear is designed to retract into the wings or fuselage, often concealed behind doors. If wheels are left partly exposed to the airstream, that's semi-retractable gear.
The retractable landing gear is primarily hydraulically operated, with only a few electrical or manual systems for small aircraft.
Pilots check the landing gear status using cockpit indicators, such as three greens or three in the green, which indicate that the nose and main gears are locked down.
Redundancy, Safety
Most modern aircraft have redundant systems in their landing gear to ensure it will work. For example:
- The Boeing 747 has four independent hydraulic systems and four main landing gear posts, ensuring a safe landing even if two gear legs are lost.
- Light aircraft possess emergency extension systems, which consist of manual cranks, pumps, acts of free fall induced by gravity, and other mechanisms to deploy the landing gear should a power failure occur.
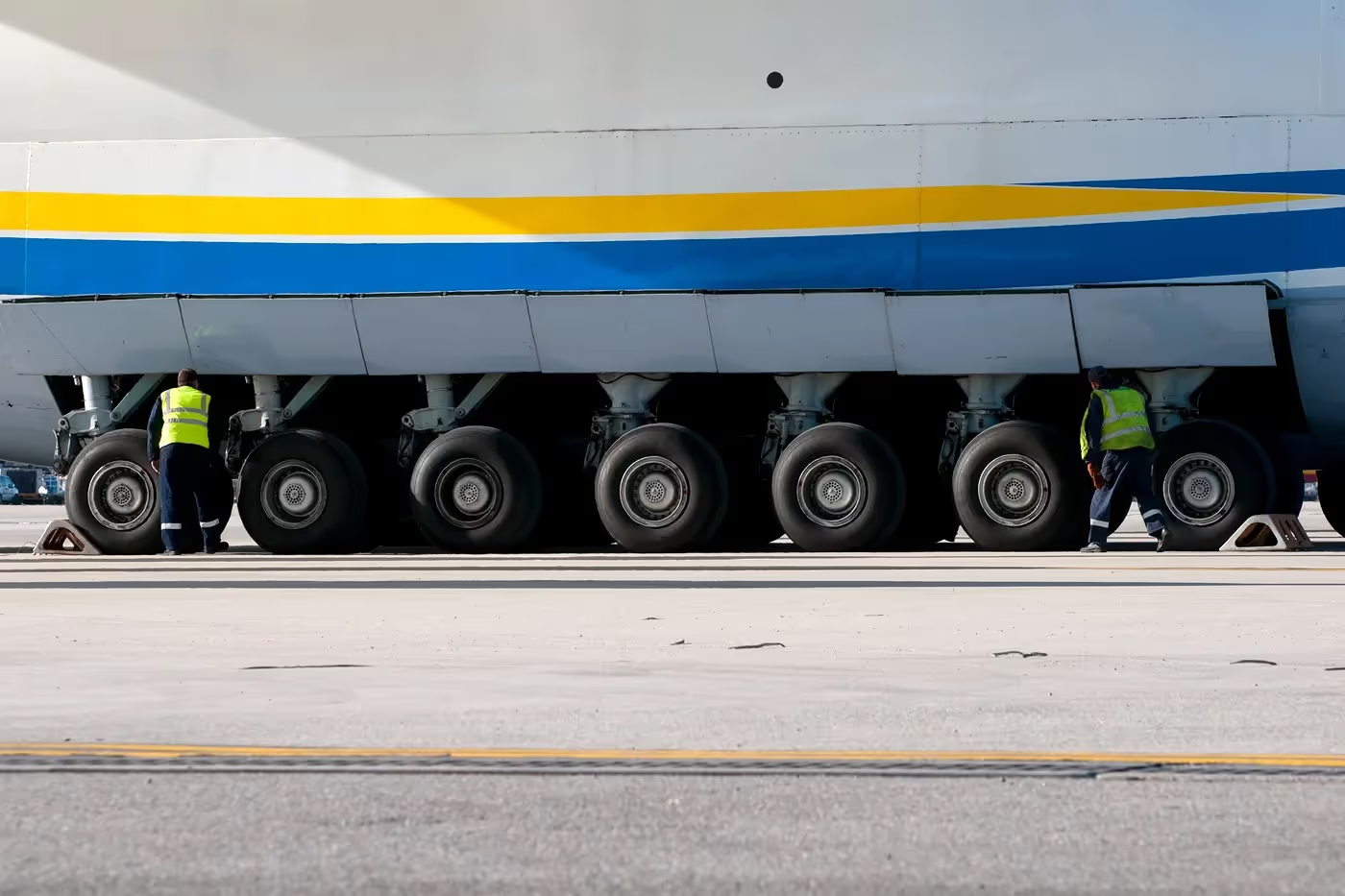
How Does an Aircraft Landing Gear Work?
The forces that act during a landing are absorbed by the landing gear, which ensures that the fuselage does not hit the ground. This is achieved through:
- Shock absorbing systems – Deploying compressible fluids within the central strut for landing force dispersion.
- Number of Wheels – Distributing the landing forces to avoid structural damage
- Retractable compartments — Concealing landing gear within the fuselage for aerodynamic efficiency.
Bigger planes have many more wheels to handle the increased weight. For instance:
- Modern airliners like the Boeing 777 utilize a tricycle configuration—featuring one nose gear and two main gear assemblies—to ensure balanced load distribution.
- Airbus A340, A380, and Boeing 747 have additional landing gear under the fuselage.
- The Antonov An-225 featured an elaborate landing gear system with 32 wheels distributed across several bogies to maximize load-bearing capacity.
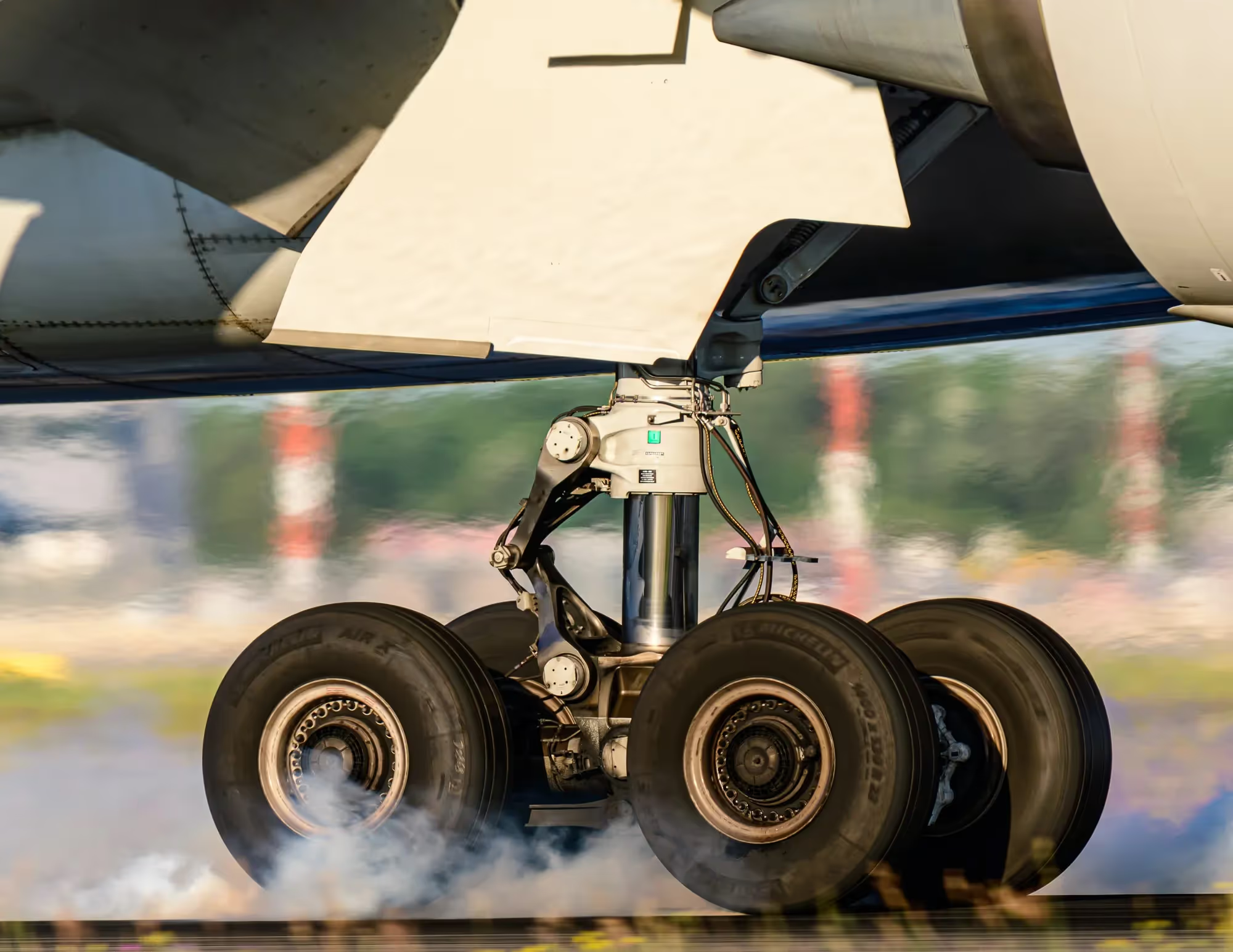
Types of Landing Gear Systems
Different landing-gear configurations serve various types of aircraft and operational requirements:
- Tricycle Landing Gear—The most popular landing gear configuration is characterized by two larger main wheels and a smaller nose wheel, allowing stability.
- Tailwheel (Conventional) Landing Gear – Less common, seen on older and smaller aircraft needing more skill to maneuver.
- Tandem Landing Gear is typically used in military and cargo aircraft. The main wheels are aligned with the aircraft's centerline.
- Multi-Bogie Landing Gear – Used in large aircraft, it spreads weight over multiple wheels to reduce runway damage.
.avif)
Landing Gear System: Component Breakdown
The following main parts comprise the landing gear:
- Strut systems – including bungee, spring, and oleo struts (which incorporate shock absorption through compressed oil and air) – work in tandem with brakes, wheels, tires, and retraction mechanisms to ensure safe landings.
- Wheels and Tires – Allow the aircraft to move during taxi, takeoff, and landing, built to endure high speeds and substantial weights.
- Brakes – To decelerate and stop the aircraft on the runway.
- Shock Absorbers – Hydraulic or pneumatic devices that reduce the forces acting during impact on landing.
- Retraction Mechanism — Stows the landing gear to minimize drag.
- Doors and Fairings — Gear protection and aero streamlining.
- Hydraulic System — Operates retraction and extension of landing gear
- Latching System – Ensures the gear stays locked in both up and down positions.
- Indicator Lights – Give the pilots visual confirmation of gear status.
- Landing Gear Control System – enables pilots to deploy and stow landing gear as required.
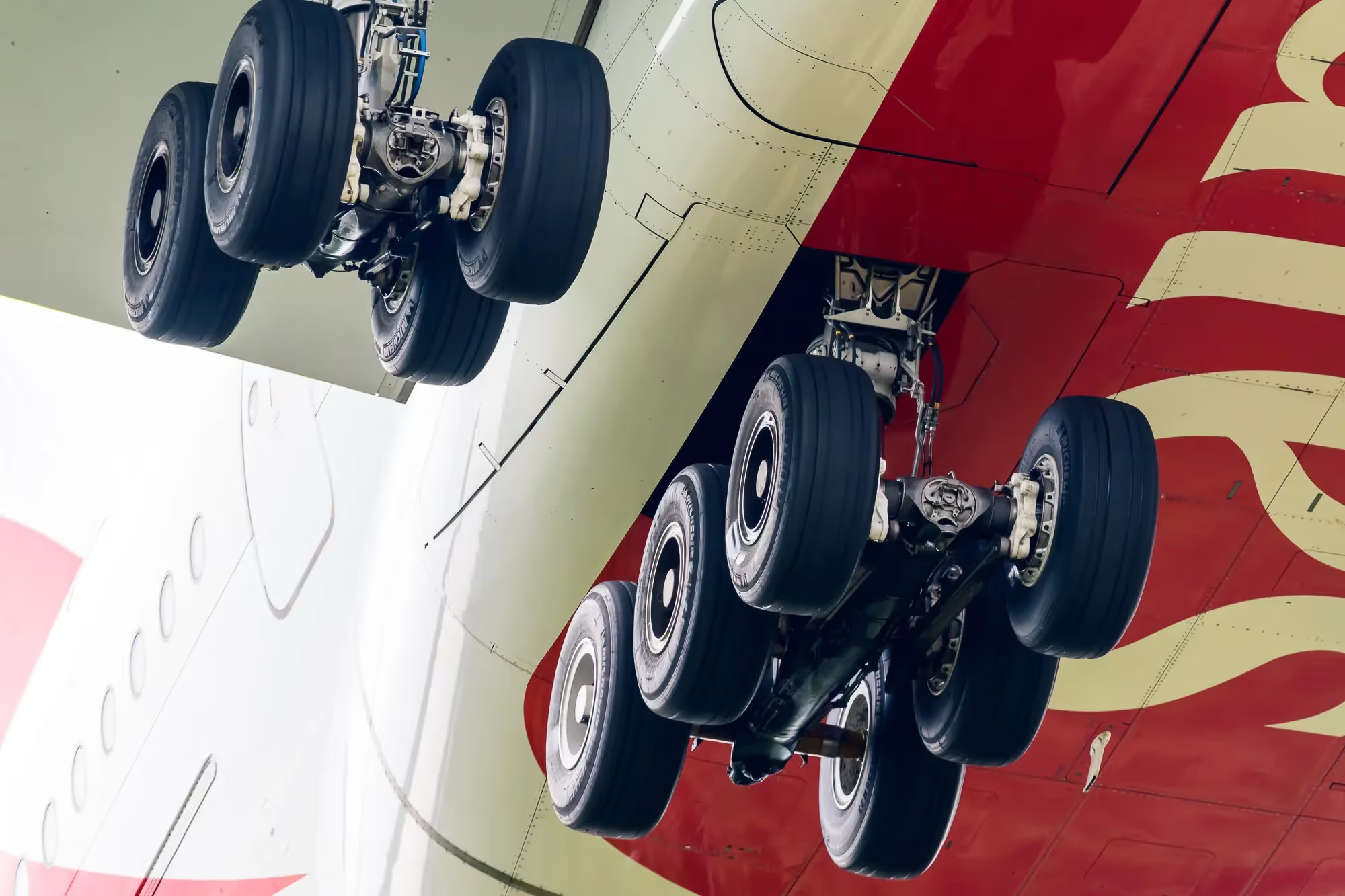
Emergency Extension Systems
To enable the landing gear to deploy in case of gear system failure, alternative systems also allow gear to be deployed from the following:
- Different hydraulic systems
- Hand-crank mechanisms
- Compressed air (nitrogen)
- Pyrotechnic discharge
- Deadweight or gravity drop systems
A free-fall system un-latches the up-lock, permitting gravity to deploy and lock the landing gear in the down position.
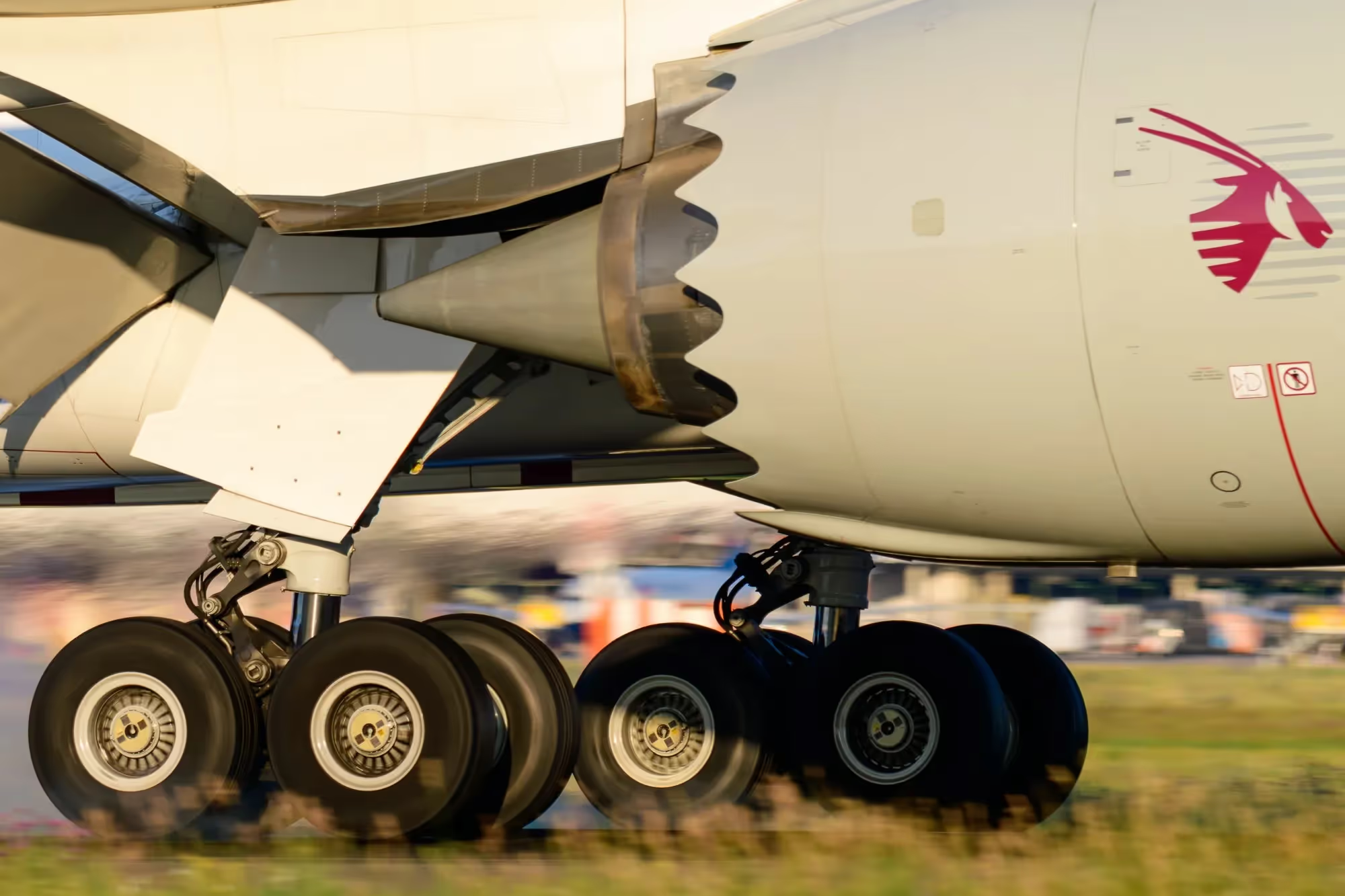
Conclusion
In summary, advancements in landing gear design—from robust materials to sophisticated retraction systems—have been pivotal in enhancing aircraft performance, safety, and efficiency.
Stay connected at every stop along your journey! Get any Saily mobile data plan at 5% off with the code AIRWAYSMAG5 + up to 5GB free!
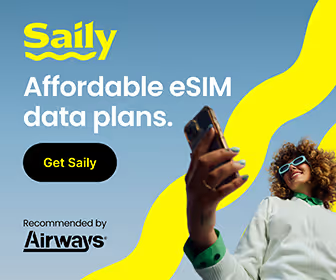