DALLAS — There’s a lot that goes on behind the scenes at an airport. While passengers hustle to board their flights or stand in line for security, there’s a small army working on the other side of the glass: ground crews, marshalers, refuelers, engineers, loaders, and tug drivers.
These people are the unseen heartbeat of aviation. They make things run smoothly, fast, and most importantly, safely. Every airline turnaround, that tight window between when a flight lands and takes off again, depends on their coordination.
On average, over 2.9 million airline passengers fly every day in the U.S. alone, according to the FAA. To support them are thousands of ramp workers who operate under strict time limits, all while ensuring they don’t compromise safety.
These teams deal with extreme weather, noise over 120 decibels, and the pressure of moving aircraft that weigh more than 100 tons. But the ramp, or apron, is also one of the most dangerous workplaces in the world.
Massive aircraft moving within a few feet of people, jet engines spinning fast enough to suck in heavy metal, cargo doors swinging open, tugs darting around, and fuel trucks sitting right next to high temperatures and rotating machinery. It’s a high-risk, high-pressure environment. That’s precisely why apron safety is such a big deal.
And when things go wrong… they can really go wrong.
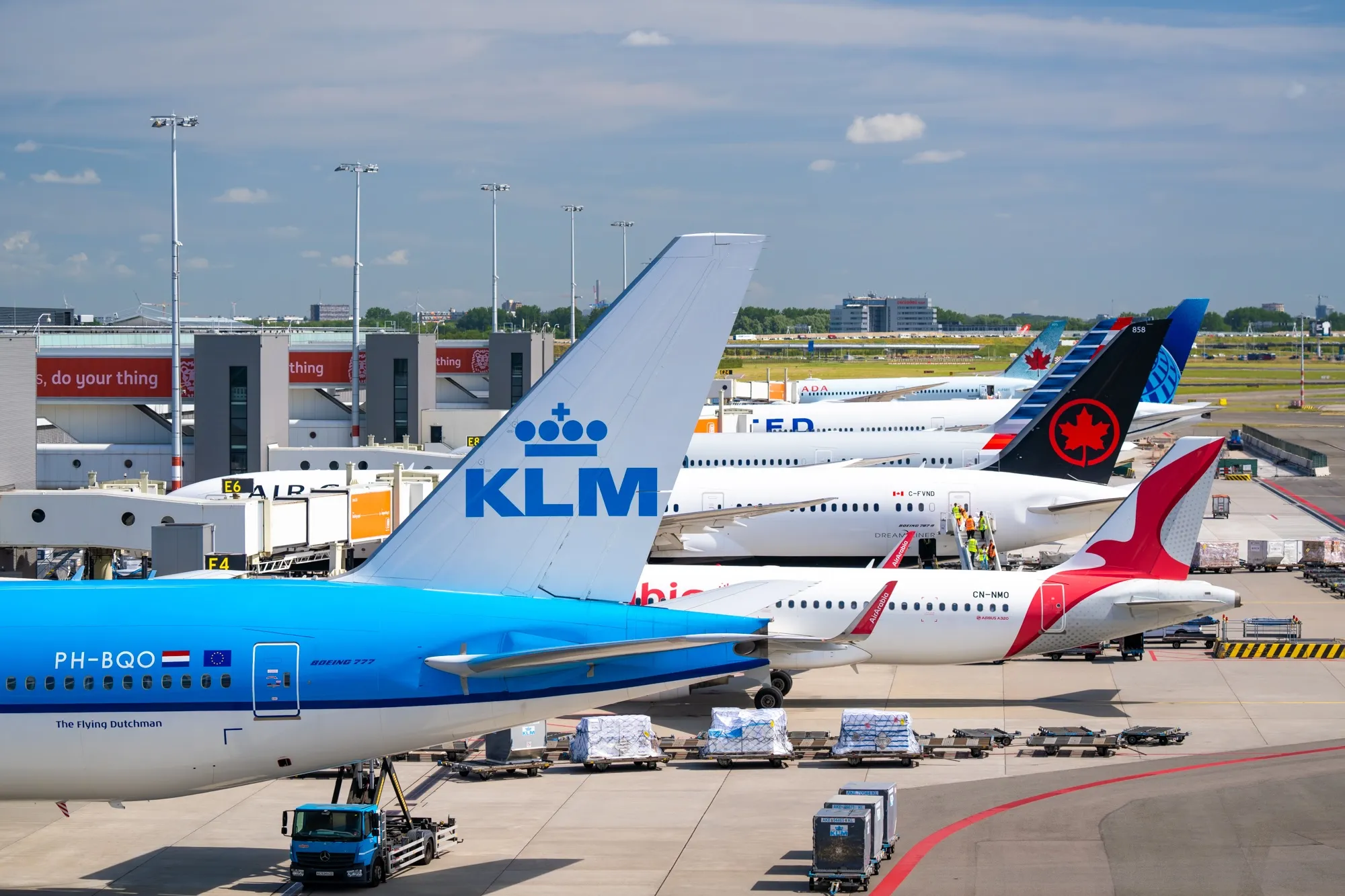
What Is Apron Safety Really About?
Apron safety isn't just about wearing helmets or fluorescent vests (though those help, too). It's a comprehensive system designed to protect ground staff, passengers, and aircraft, particularly when aircraft engines are running or when planes are taxiing.
According to the International Air Transport Association (IATA), apron-related incidents cost airlines more than US$10 billion annually due to damage and injuries. That number highlights the high stakes, not just in terms of lives lost, but also in terms of equipment damage and disruption to normal operations.
The apron is the area where the aircraft parks, loads, unloads, refuels, and gets serviced. It’s one of the most active places in an airport. Safety protocols here cover a wide range of activities:
- Marshalling and guiding aircraft to and from parking bays
- Keeping safe distances from engines and propellers
- Ground vehicle movement coordination
- Fueling safety (FAA fueling guidance)
- Engine cooldown procedures
- Human movement and visibility on the tarmac
- Communication between the cockpit crew and the ground staff
These rules aren’t just there for the sake of paperwork. They’re reinforced through hands-on training, regular safety checks, and daily briefings before each shift. And some airports are pushing even further by introducing new technology that actively tracks what’s happening out on the ramp.
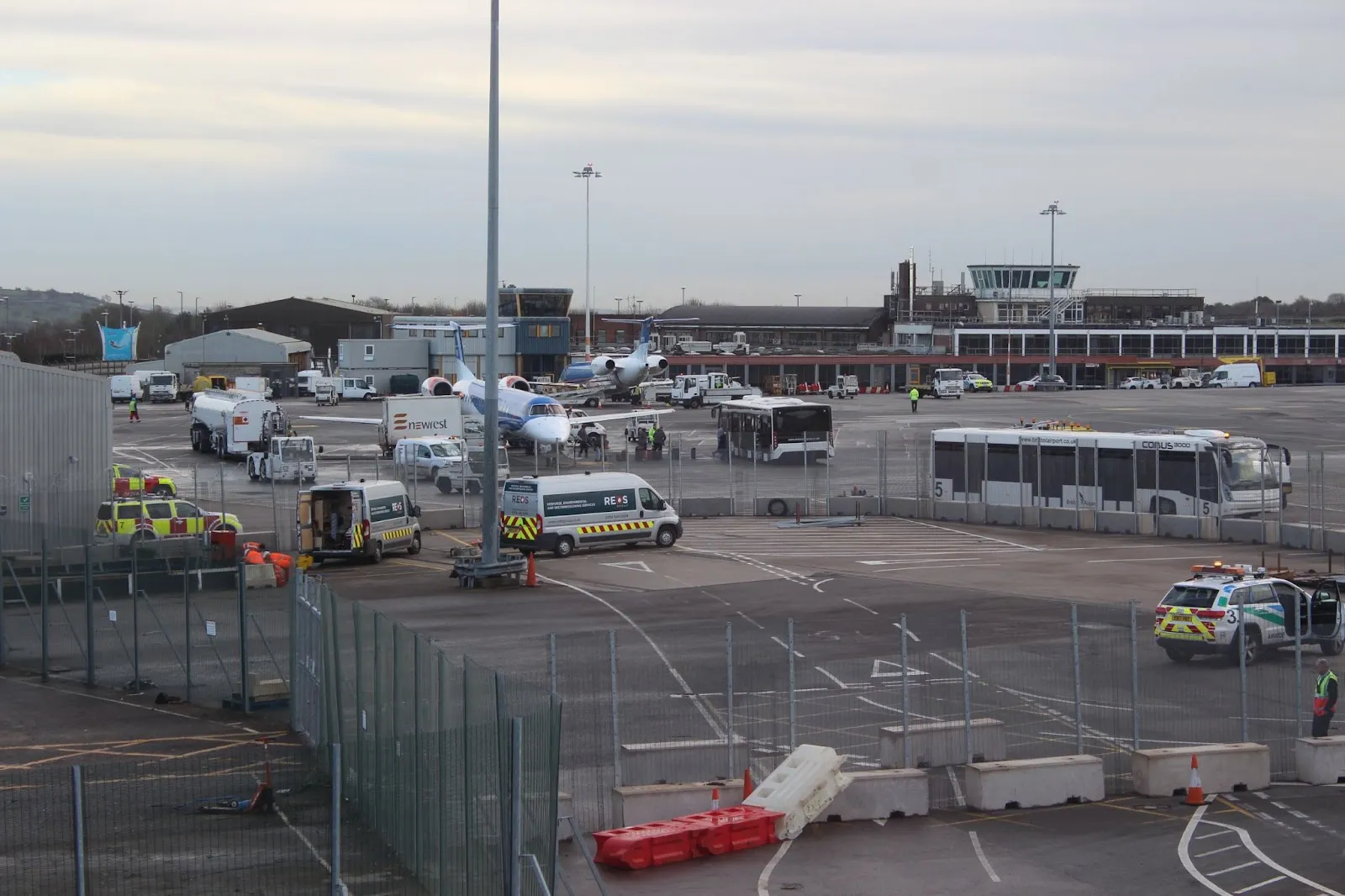
At Rome Fiumicino (FCO), ApronAI has been installed across 57 gates to monitor turnarounds and flag any discrepancies. Toronto Pearson (YYZ) rolled out the same system across all 100-plus gates, giving ground crews live updates on delays or missed steps.
Las Vegas (LAS) joined in last year, connecting ApronAI to its Aerobahn platform so that both apron supervisors and airline ops can keep a closer eye on what’s moving and what’s not. Even airlines have been involved; Air New Zealand (NZ) utilizes this technology to help track more than 50 coordinated activities at Auckland Airport (AKL), which makes operations easier, more efficient, and, most importantly, safer.
Still, it doesn’t mean the human element has taken a back seat. There’s background noise, limited visibility, and the constant pressure to meet tight departure windows. Even with all the tech watching over things, it’s the people on the ground who keep things safe.
You need to know your place on the ramp, understand the timing of each step, and be ready to act when something changes. A fuel truck may show up late. An engine may start sooner than expected. In those moments, all the software in the world can’t replace a sharp pair of eyes and a clear head.
And it’s not just up to the ramp crew. Pilots, cabin staff, and tower controllers also have their part to play. Safety on the apron depends on everyone sticking to the plan. One slight misstep or late call can throw the whole thing off.
The Harsh Reality: People Pulled Into Jet Engines
But what happens when things don’t go as they were supposed to? Let’s not sugarcoat it; there have been horrifying incidents where ground workers were sucked into operating engines. These events, although rare, shake the entire aviation industry each time they happen.
The effects ripple through every level, from operations teams to regulatory bodies. The most disturbing part is how preventable some of these incidents are, often triggered by small misjudgments or miscommunication during high-pressure moments. Let’s take a look at some of these incidents closely:
Tragedy at Milan Bergamo Airport: Investigations are underway. On July 8, 2025, a tragic incident occurred at Milan Bergamo Airport (BGY). A man ran across a restricted area of the apron and was pulled into the engine of a Volotea (V7) Airbus A319 that was about to depart for Asturias. CCTV later showed him sprinting past airport security, and while the whole picture isn’t clear yet, early signs suggest it might’ve been a suicide attempt, not a failure in standard ramp safety.
The flight was stopped immediately. Everyone on board was safe, but it shook the entire operation. Emergency crews arrived, and investigators were summoned immediately. Support was offered to staff and crew who witnessed it. Even though this case appears to be an intentional breach, it still highlights the importance of constant alertness and robust access control on the apron.
The 2023 Montgomery Incident: A Shock for the U.S. Aviation Community. In January 2023, at Montgomery Regional Airport (MGM) in Alabama, a Piedmont Airlines (PT) employee, Courtney Edwards, died in a similar accident. She was working on an American Eagle (MQ) Embraer 170 that had just arrived from Dallas (DFW), with one engine still running during its cooldown phase.
While the plane was parked at the gate, Edwards got too close and was pulled into the active engine. Later reports revealed there had been miscommunication about when it was safe to approach the aircraft.
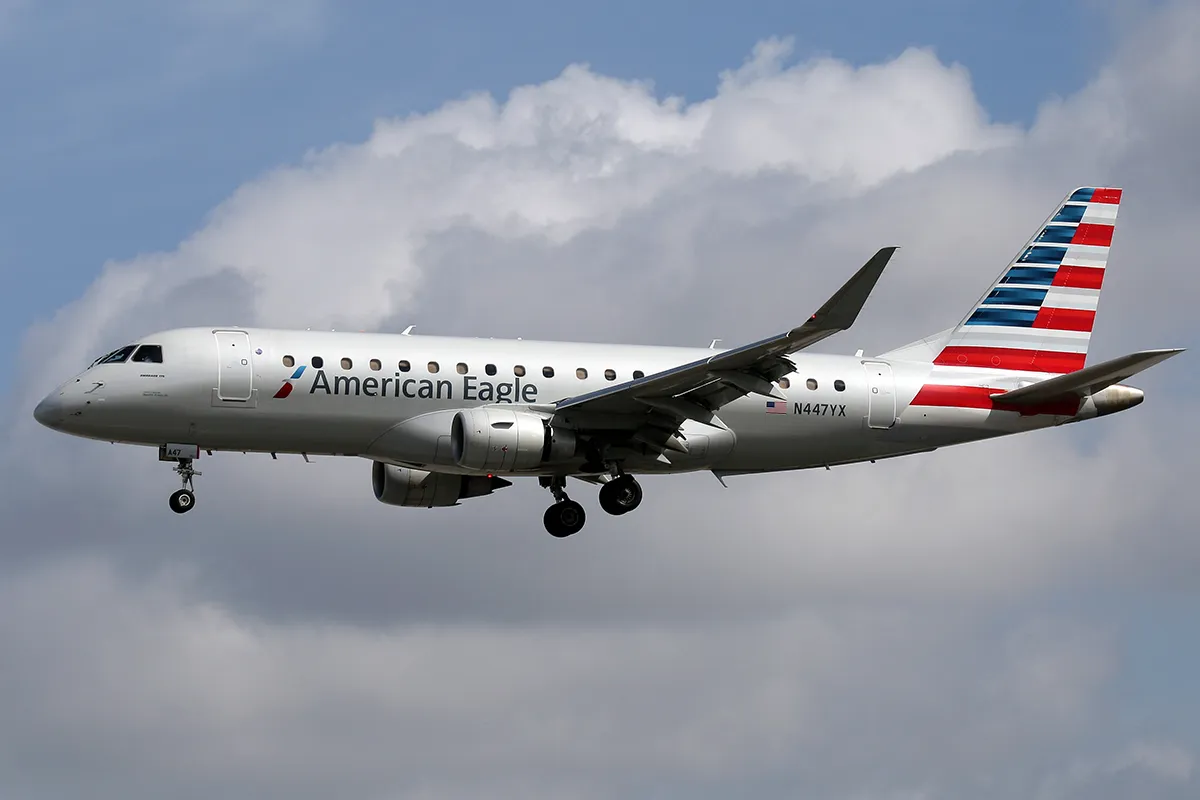
The NTSB concluded that, although the aircraft's systems were functioning normally, the employee entered the danger zone too early. This engine, a GE CF34-8E, creates powerful suction even at idle, and the required 15-foot safety distance wasn’t maintained.
Reports also suggest that she was constantly warned about the dangers of working near an aircraft just after it lands. It wasn’t just one person’s mistake; it was a breakdown in safety communication and operational discipline.
Mumbai, 2015: Another Preventable Loss: A similar event occurred in India in 2015 at Mumbai Airport (BOM). A technician from Air India was tragically sucked into the engine of an A319 while performing a routine check. The aircraft had been cleared to push back, and the engine was powered on, but the technician was too close at the wrong time.
Reports from the Aircraft Accident Investigation Bureau (AAIB) indicated that the technician was communicating with the cockpit when the engine started up prematurely. Witnesses claimed there was confusion about the pushback clearance, and the technician may have assumed the engine was off while the pilot started the engine.
DGCA also released their final report two years later and concluded the cause of the accident: “Non-adherence to Standard Operating Procedures (SOP) & delayed departure of flight due to improper rostering of crew resulted in the accident.
Such incidents often stem from simple lapses in cockpit-ground crew synchronization, sometimes exacerbated by noisy ramp conditions or outdated communication tools. These stories are not just tragic; they’re wake-up calls that show how vital every detail is in apron operations.
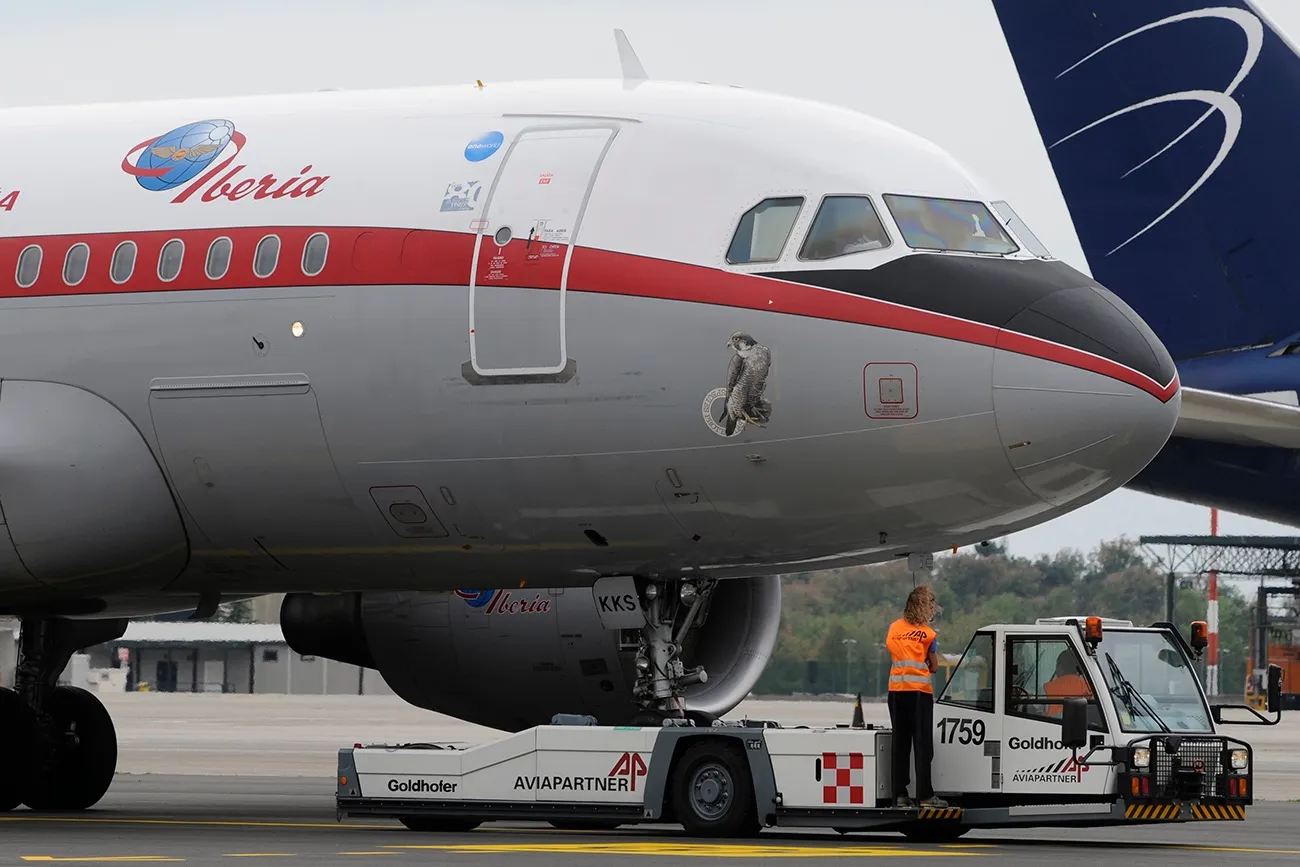
So, Why Do These Incidents Still Happen?
It's easy to assume that ground crew members are careless when these things happen, but the reality is more complex. Accidents on the apron usually involve human factors, not just negligence. Even with all the rules, training, and signage in place, it only takes one second of distraction or one step too close to trigger disaster. Safety culture isn’t just a checklist; it’s an attitude that must be reinforced constantly.
1. Fatigue and Long Shifts: Many ramp workers work odd hours, overnight shifts, split rosters, and sometimes in extreme weather. Fatigue affects judgment, reaction time, and the ability to focus on details. Fatigue is one of the most significant hidden risks on the ramp.
Some reports have shown that human factors, such as exhaustion, time pressure, and distraction, regularly play a role in ground incidents. When you're running on fumes, it only takes one missed step for things to go sideways.
2. Inadequate Training or Briefings: In some incidents, the staff weren’t informed that the engine was still running, or weren’t trained properly on safe distances. Budget constraints and high turnover can lead to rushed onboarding, especially with contracted ground services.
3. Lack of Visual Cues or Apron Design Flaws: Not all aprons are well-designed. Poor lighting, confusing ground markings, or missing safety cones can make it hard for staff to know where they should or shouldn't be. A 2023 review by the National Academies also highlighted the lack of standardized apron designs across U.S. airports, which leads to confusion and increased risk, especially for new or temporary staff unfamiliar with the layout.
4. Breakdown in Communication: Miscommunication between the cockpit and ground crew can have deadly consequences. The ICAO recommends “positive clearance” protocols, but in busy conditions, those protocols sometimes fall through the cracks.
5. Over-Familiarity or Complacency: Sometimes, workers are so used to being around aircraft that they start cutting corners. Supervisors often have to fight complacency by implementing random checks, safety walks, and reinforcing policies.
.webp)
Human Factors and Apron Design
Most modern airports are trying to address these risks through better apron design and a deeper understanding of human behaviour. It's not just about rules; it's about making the environment safer by design:
- Marking “nogo zones” has gone high-tech: Airports have shifted from faded lines and cones to LED-lit perimeters, bright paint, and barrier flags around jet intakes or pushback paths. These visual cues comply with FAA standards that require unmistakable hazard markings, and many hubs have rolled out these enhanced safety zones across their aprons.
- Engine run-up enclosures, or “hush houses”, are also evolving: Oakland International (OAK) recently reopened its GRE with updated noise- and hazard-containment systems. The walls now reduce decibels by around 17 dB, helping to protect maintenance crews during high-thrust engine tests without interfering with apron activity.
- Technology is transforming apron operations too: Frankfurt Airport (FRA) is rolling out ADB Safegate’s latest Safedock X system, replacing older guidance units across all gates. By mid-2026, the airport will feature 117 of these systems, which combine radar, laser, and camera sensors to precisely guide aircraft into parking slots, minimising ground crew exposure.
- Even equipment placement is getting smarter: Following IATA’s ISAGO safety audits, many airports are moving carts, GPUs, hoses, and other support gear away from engine danger zones so crews can work without stepping into high-risk areas.
- Noise safety is improved by better headsets: New noise-cancelling aviation headsets from Honeywell and others suppress harsh frequencies while keeping communication clear, ensuring vital radio messages don’t get lost in the engine roar.
- Virtual ramp training is cutting real-world mistakes: More airports and ground handling firms are using virtual reality to prep staff for high-risk apron scenarios, like guiding aircraft, avoiding jet blast, or spotting FOD. These VR modules allow trainees to practice in realistic conditions without facing real-world danger.
Operators like Lufthansa (LH) and ANA (NH) have introduced this technology, which significantly enhances efficiency and safety, thanks to improved muscle memory and sharper reflexes in high-pressure situations.
These improvements may not be cheap, but they save lives.
Looking Ahead
Apron safety isn’t just about ticking boxes or adding new tech. It’s about understanding how people move, react, and make decisions under pressure and then designing the environment around that.
As airports become busier and aircraft become larger, the risks multiply. However, with more innovative layouts, better training, and tools that work in harmony with humans (not against them), we’re witnessing a shift from reactive safety to proactive design. It’s not perfect yet, but the focus is moving in the right direction, towards a ramp that protects its people as much as it moves planes.
Stay tuned and keep following Airways. Follow us on LinkedIn and Instagram for the latest updates as well!