DALLAS — The fuel system onboard an aircraft is one of the most critical, whether it is a Cessna 152 out for training or a Boeing 777-300ER crossing the Atlantic Ocean.
Perhaps overlooked by us aviation geeks, understanding the fuel system is highly crucial. As part of a sequence of moving, storing, channeling, and distributing the fuel, or controlling pressure and temperature, the fuel passes through several subsystems and components before being burned in the engine's combustion section.
All processes must be carefully monitored to ensure mechanical efficiency and safety. The system is monitored by several gauges, transmitters, and sensors to ensure that fuel levels are read at all times, regardless of the flight phase. This article explains the aircraft fuel system, including its layout, elements, and how innovation contributes to safety and reliability.
Fuel Storage Tanks, Venting Systems
In most large aircraft, fuel is primarily contained in the wings, but center tanks are also present in the fuselage. Wide-body jets could also feature tail or horizontal stabilizer tanks to help manage the plane’s center of gravity on long-range flights, known as trim tanks, which are also found on the Airbus A330-200 and A330-300. This is an additional option offered by Airbus.
There is a dual purpose to the fuel stored in the wings: it provides fuel to the engines and reduces the bending stresses on the wings during flight. The center tanks, located in the middle, are consumed first, and the wing tanks are utilized secondarily. In aircraft with both inner and outer wing tanks, the tanks are usually emptied from inboard first to maintain the wing's strength.
Just as important is ventilating the fuel tanks. Surge tanks, which discharge into the main tanks through vent pipes, are used to catch overflow generated during complex maneuvers and return it to the main tanks by gravity when the aircraft resumes horizontal flight. Furthermore, the surge tanks are vented to the atmosphere and flooded in the case of air overflow, and are pressurized with ram air to maintain a positive pressure within the tanks.
This pressure prevents fuel from vaporizing too much at high altitudes, and at the same time, the fuel temperature remains below the boiling point, regardless of whether there is heat or not. It also eliminates the vacuum inside the tanks during the high fuel flows demanded by the engines (Simple Flying).
Inner Workings of the Fuel System
The journey of fuel is a carefully choreographed dance from tanks to combustion chambers:
- Booster pumps are located inside the tanks that circulate and push the fuel toward the engines. Pilots electrically control them.
- Each tank consists of two pumps, ensuring a backup is present in case one pump stops working.
- The fuel passes through a low-pressure (LP) fuel valve before it enters the engine-driven pumps. The LP valve is often referred to as a spar valve.
- Depending on the aircraft design and system, the ED pumps can include LP and HP stages.
Below is a schematic of the fuel system found onboard an Airbus A320.
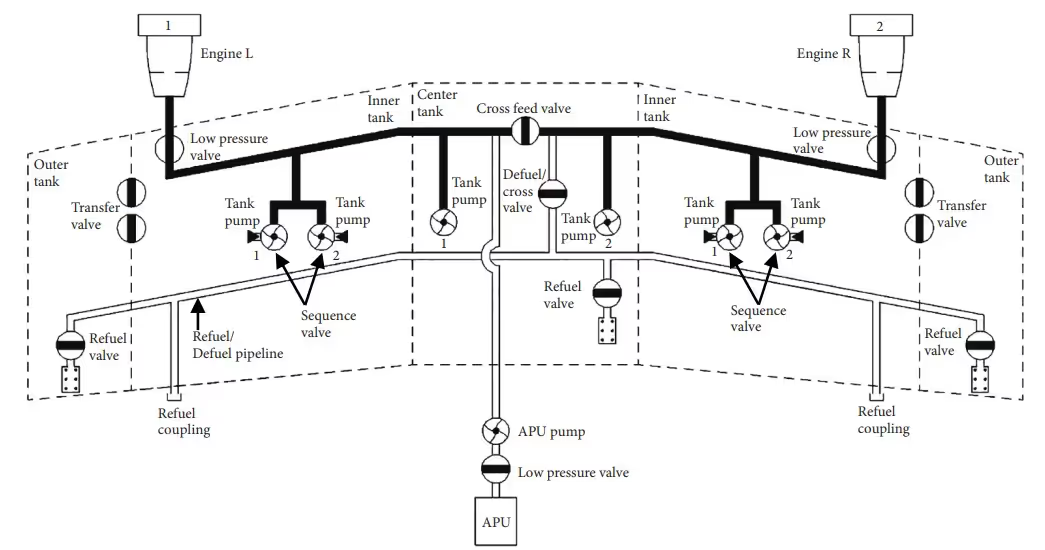
As the aircraft gains altitude, booster pumps become essential to use due to the low ambient pressure outside, which causes the fuel to vaporize quickly and can block the fuel lines, a phenomenon often referred to as vapor lock. In case the booster pumps fail, suction valves come into play where they automatically suck fuel into the engines however this requires the aircraft to descend to a lower altitude.
Before the fuel enters the engine's combustion chamber, it must go through strict filtration and temperature control steps to ensure that the fuel entering is clean of contaminants and warm enough to prevent freezing or waxing. This is done by fuel or oil heat exchangers and fuel filters.
Once the fuel is free of contamination and warm enough, HP pumps direct the fuel to nozzles that spray fuel at specific intervals to ignite. Fuel is also used by hydraulic systems in the engine to operate components, such as variable stator vanes, and to cool integrated generators.
Fuel is always routed symmetrically onboard an aircraft, meaning that the left-wing tank supplies fuel to the left engine and the right-wing tank supplies fuel to the right engine. In case there is a fuel deficiency, cross-feed valves are present that can be manually or automatically operated to supply fuel to the tank that is low on fuel, restoring balance and maintaining safe operation.
The Auxiliary Power Unit (APU) is also a small turbine engine that needs fuel to operate. It has dedicated fuel pumps that direct fuel to the APU, keeping it running. The APU provides electrical and pneumatic power during both flight and on the ground. For example, the Airbus A330-200 has two dedicated forward and aft boost pumps that supply fuel to the auxiliary power unit (APU).
Refueling Procedures
Modern commercial aircraft typically use pressure-fueling systems, where the fuel hoses connect to refueling couplings located under the wings or the belly of the fuselage.
The refueling panel allows the operator to set the predetermined fuel load. Refueling then proceeds automatically, filling the outer tanks first (to reduce stress on the wings) and then the inner and center tanks.
Aircraft are also equipped for manual (gravity) refueling through points located at the top of the wings. This is a slower process, yet still useful when pressure-fueling systems are not available. In gravity refueling, operators first fill the wing tanks, maintaining the aircraft's balance, before refueling the center tanks. In simpler terms, commercial aircraft use pressure refueling while general aviation aircraft use gravity refueling.
Measuring Fuel Quantity
Currently, capacitive probes are used in modern aircraft fuel systems to measure the quantity of fuel:
- Capacitors, made out of two plates powered by an AC supply, are installed in the tanks.
- The flow of current depends on the dielectric constant, which varies depending on whether the space between the plates is filled with air, fuel, or a mixture.
- A change in dielectric constant provides very accurate measurements.
However, fuel density decreases with temperature, and thus, the system's accuracy is temperature-dependent. Compensator probes have been installed in tanks to automatically correct density changes based on temperature readings, ensuring reliable data for pilots at all phases of flight.
Safer Flights with Aircraft Nitrogen Generating Systems for Fuel Tanks
Why Fuel Tank Safety Matters
The risk that fuel tank fires pose is unarguably critical in aviation. Perhaps the most unfortunate of all has to be TWA Flight 800 in 1996, which saw the loss of all 230 souls onboard the TWA Boeing 747 when a spark ignited in an almost empty center fuel tank, resulting in an explosion.
Consequently, the Federal Aviation Administration and other regulatory authorities required aircraft manufacturers to install devices to reduce the risk of spark or flame ignition at the point of use through inerting systems.
In fuel inerting, the oxygen in the fuel tanks is displaced or replaced with an inert gas, such as nitrogen, which prevents combustion from happening relatively. Why nitrogen? Because it is the most common gas found in the atmosphere, comprising 78%.
Nitrogen Generation Systems (NGS)
Nitrogen Generation Systems (NGS) are systems used to produce either pure nitrogen or nitrogen-enriched air (NEA) to displace oxygen in fuel tanks. The systems operate on a principle similar to the fire triangle: fire requires fuel, heat, and oxygen. If you take away oxygen, the triangle collapses, and therefore, the fire is controlled.
It is paradoxically very heavy and inert (or not reactive) in relation to oxygen. So, it serves well to displace and dilute the dangerous oxygen present in aircraft fuel tanks. (According to Generon).
How Aircraft Fuel Inerting Systems Work
The FAA prefers the inerting method for fuel tanks to include Onboard Inert Gas Generation Systems (OBIGGS), which incorporate Air Separation Modules (ASMs). The system works by,
- Taking bleed air, which is compressed air from the compressor section of the engine, to the ASM.
- Use of either semi-permeable membranes or carbon molecular sieves to separate nitrogen from oxygen.
- Nitrogen-rich air will then be directed into the fuel tanks, where it is mixed with oxygen at a concentration of less than 12%, making it non-combustible.
Below is a schematic and working flow of the NGS system.
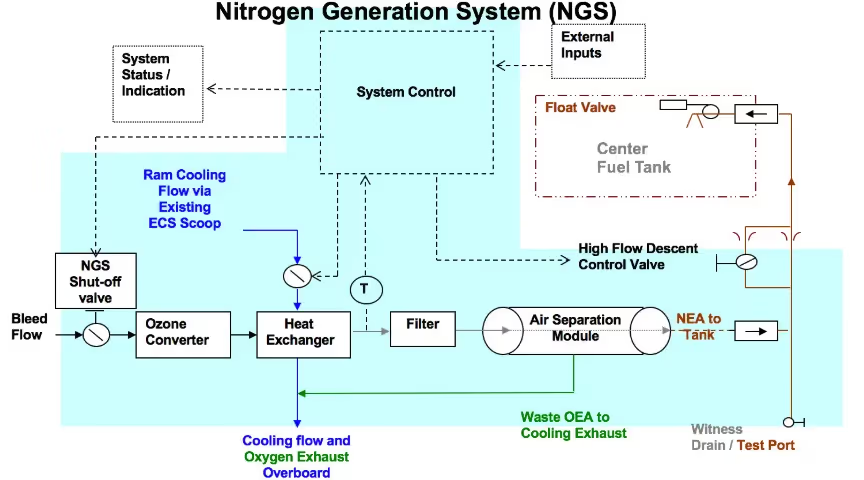
Such a system would operate continuously through the flight period and help ensure safe levels of oxygen concentration across all altitudes and temperatures (GEneron).
Five Major Benefits of Aircraft NGS Systems
- Cost-Saving: They generate nitrogen on-site, taking air from the atmosphere, so there is no maintenance cost involved.
- Efficient: Absolute purity of nitrogen produced without moisture and any foreign substances.
- Safe: There is no need to store high-pressure nitrogen cylinders, which reduces hazards.
- Reliable: A long lifespan and minimum-maintenance operation.
- Environmentally Friendly: Reduces the environmental footprint by two-thirds in terms of production and transportation compared to conventional liquid nitrogen. (As per Generon)
Stay connected at every stop along your journey! Get any Saily mobile data plan at 5% off with the code AIRWAYSMAG5 + up to 5GB free!
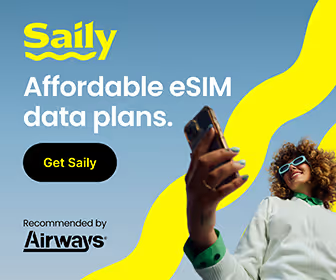