DALLAS — The future of aviation revolves around sustainability. But building a greener, more environmentally friendly industry is nothing new.
Engine makers are a prime target for reducing aviation's impact on the planet. As well as reducing emissions from their power plants, they must also strive to reduce fuel burn, thus reducing costs for their airline customers.
Over the years, there have been various innovative designs, one of which was the 'Prop-fan/Unducted fan,' also known as an 'Open Rotor Engine.'
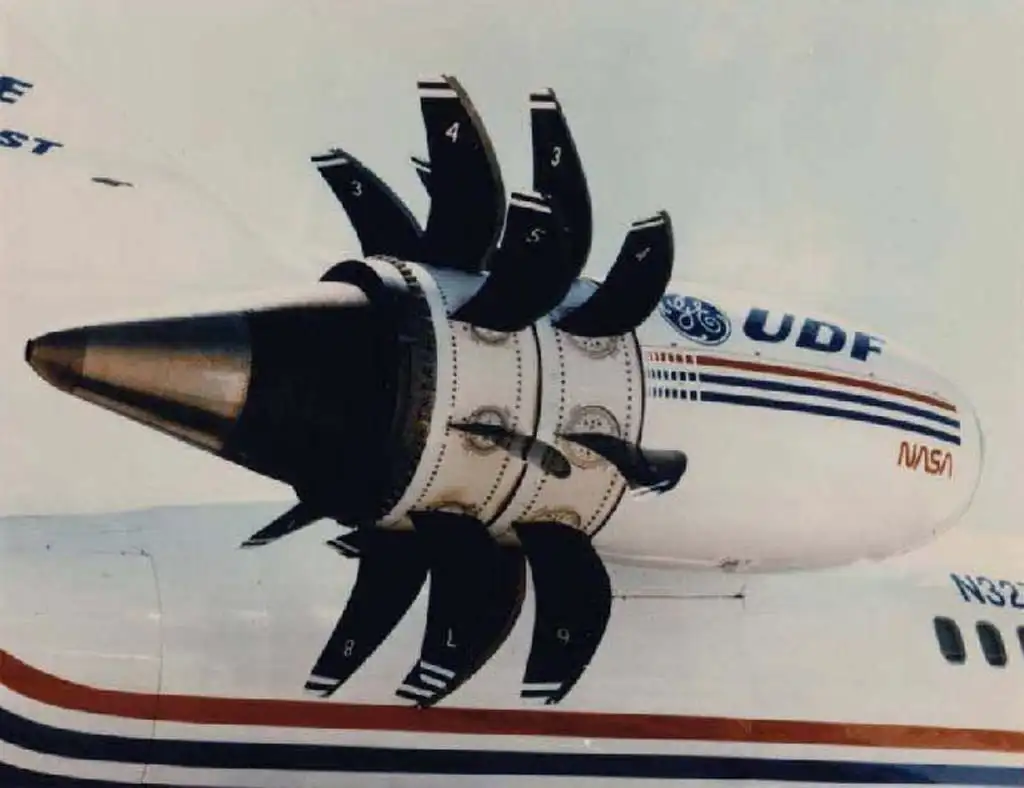
Early Days
Back in the 1940s, American propeller maker Hamilton Standard looked at creating new blades so that its power plants could match the performance of the emerging turbofan/jet engines. Sadly, noise levels, blade stress, and flutter issues caused the concept to be dropped.
The crippling oil crisis of the 1970s led airlines to call upon plane makers to develop new technology to reduce their costs. Led by the US space agency NASA, teams began looking at installing a more fuel-efficient propellor that could operate at the same speed and altitude as a jet engine.
In October 1975, the 'Advanced Turboprop Project' was announced, promising a massive fuel saving of 30 to 35%. Development continued, albeit at a slow pace, and in 1981, Hamilton Standard was given a contract to produce a full-size working version called the SR-1.
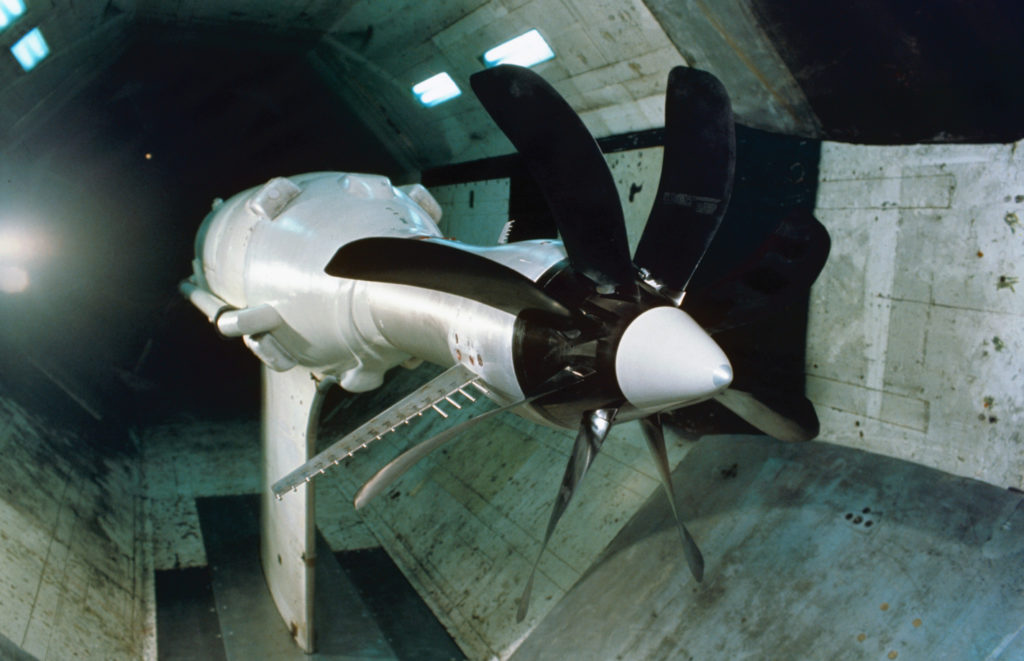
Drawing Board to Reality
Utilizing the initial test work done by NASA, General Electric (GE) began developing its own Unducted Fan Engine (UDF), the GE36, in 1982. Promising a 30% reduction in fuel burn without decreasing inflight cruise speeds, NASA awarded GE a US$20.4 million contract in February 1984.
Boeing agreed to utilize one of its 727-100s (N32720) as a testbed for the GE36. Its first flight took to the skies on August 20, 1986. Numerous test flights were carried out with the power plant achieving a cruise speed of Mach .84 at an altitude of 39,000 feet.
Meanwhile, engine rival Pratt & Whitney (P&W) had teamed up with Allison Engine Company which had been developing its own UDF, the Model 578-DX.
Attached to a Gulfstream II, the 578-DXs first flight took to the air on March 28, 1987. An extensive test program ensued with 73 flights over 133 hours, costing an estimated US$56 million.
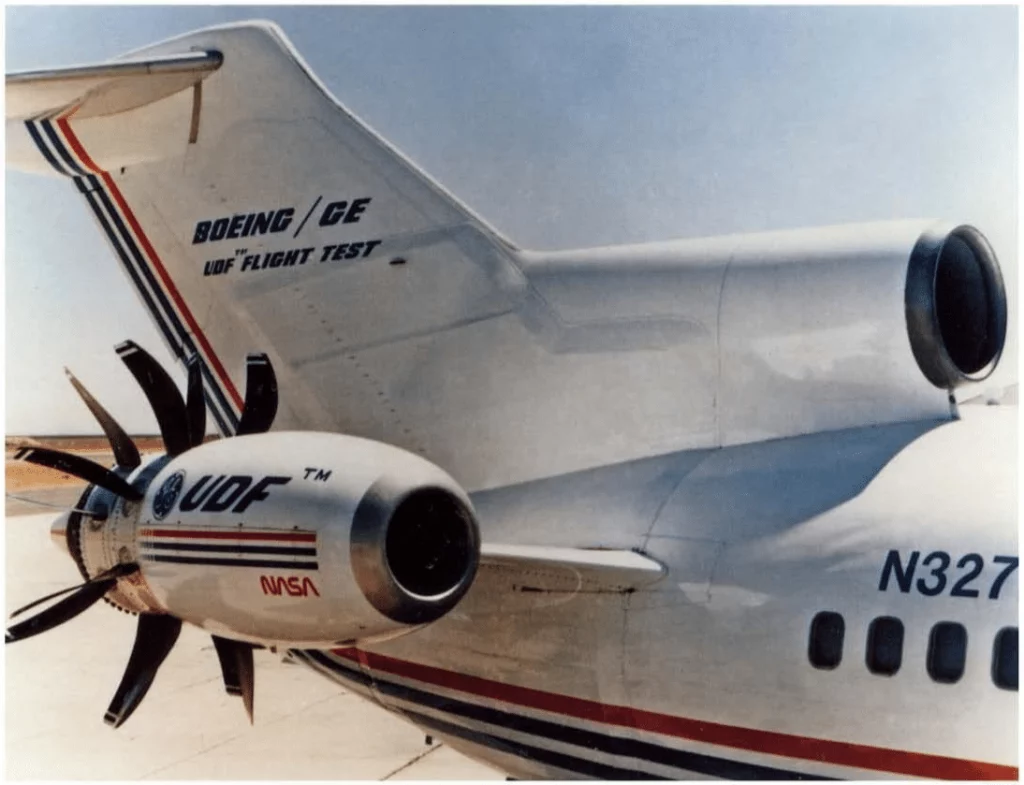
Boeing Vs. McDonnell Douglas
These new engine types came when plane makers sought to develop new fuel-efficient airliners.
Boeing had officially launched its 7J7 program at the 1985 Paris Air Show, the same show where GE and P&W were showcasing their UDF engines.
While GE and P&W had been developing Propfan engines to be located at the rear of the fuselage, International Aero Engines (IAE) was studying a design that could be housed on the wing.
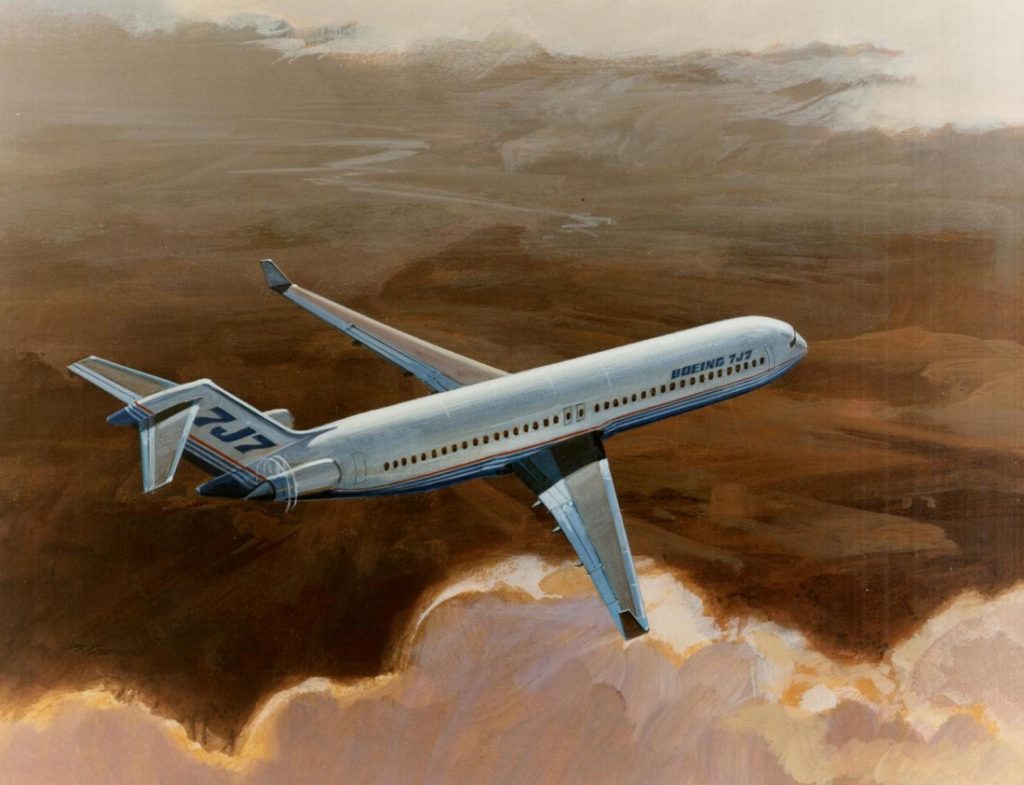
The IAE V2500SF 'SuperFan' was launched in July 1986, and by December that year, the manufacturer had offered the type to Airbus to power its new A340 jets. Orders came, with Lufthansa (LH), Alitalia (AZ), UTA (UT), Sabena (SN) and Finnair (AY) all opting for the engine. Airbus also planned on using the V2500SF for its A320 aircraft and Boeing added the power plant into the mix for its 7J7s.
Meanwhile, McDonnell Douglas (McD) was developing two Propfan variants of its MD-80, the MD-91X, and the MD-92X. The 100-150 seat aircraft were mooted to enter service in the early 1990s, and marketing for the new aircraft began in 1985.
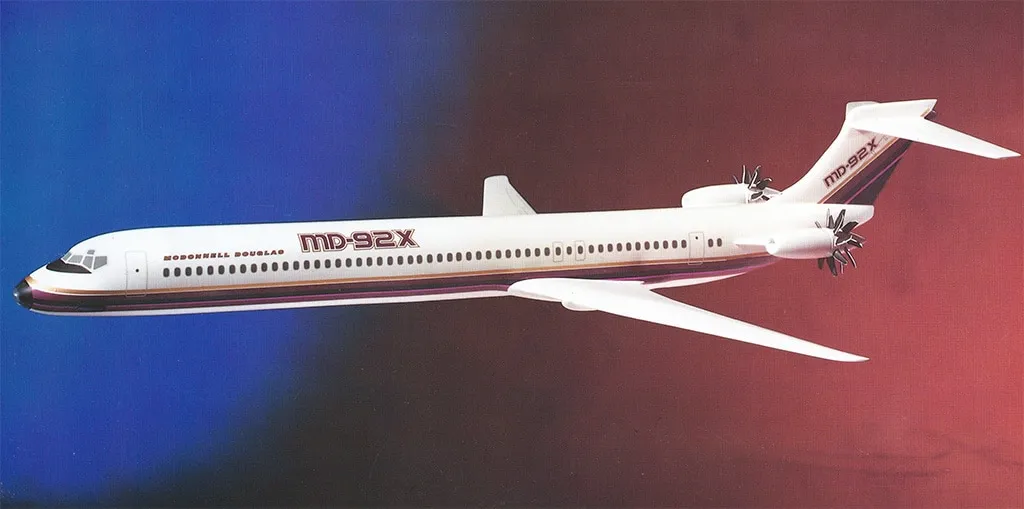
Facing Headwinds
But doubts about the viability of UDF engines were increasing. P&W was running massively behind schedule with its Model 578-DX. In April 1987, IAE canceled its 'SuperFan' project altogether. This subsequently led Boeing to delay its 7J7 project indefinitely in December 1987.
But McD pressed on with plans to use both the GE and P&W engines on its next-generation airliner. It modified one of its MD-80 jets with a GE36 power plant in 1987.
The aircraft carried out one hundred and sixty-five hours of testing over 93 flights. The results were promising, and McD even began discussing offering retrofits to its existing MD-80 airframes. It also looked at a military variant of the MD-91. Known as the Long-Range Anti-Submarine Warfare Capable Aircraft (LRAACA), it would replace the US Navy's P-3 Orion aircraft.
In September 1988, McD flew its UDF prototype to the Farnborough Air Show in an attempt to garner sales. But the moment had passed. Despite finally managing to add a prototype PW-Allison 578-DX to an airframe in early 1989, in May that year the manufacturer decided to terminate the MD-9X project and with it, the Propfan engine dream.

Part of the reason was the continued delays with P&W's engine that would delay the aircraft's launch. GE was also unprepared to develop its GE36 further until McD had at least 150 firm orders.
Another major issue was that oil prices had begun to drop dramatically when these new engines finally flew. Therefore, fuel costs were no longer seen as an issue for airlines. Propfans were also up to 40% more expensive than the turbofan engines it hoped to replace.
McDonnell Douglas thought it was the future of its airliners. Boeing wanted it for a unique new jet. Global airlines liked its massively reduced fuel costs. But sadly, engine manufacturers couldn't make the propfan work.
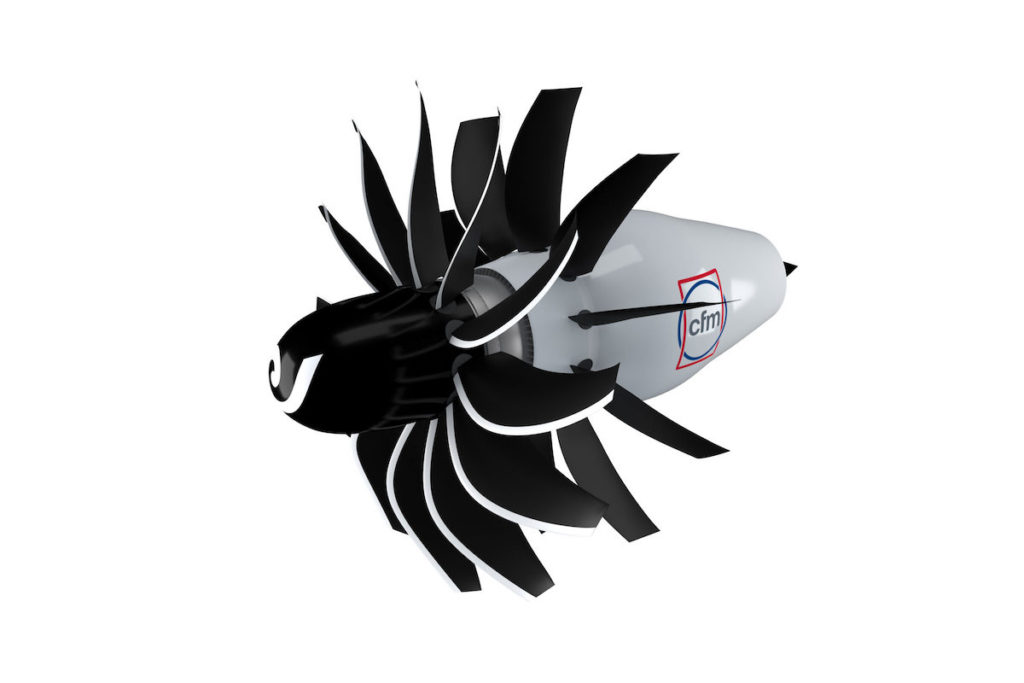
The Future
Despite dropping the UDF program, GE utilized its findings to develop composite fan blades for the mighty GE90, which, when introduced by British Airways (BA) on its Boeing 777 fleet in November 1995, was the world's largest jet engine.
Numerous other plane makers looked at using Propfan engines to varying success. The Ukrainian manufacturer Antonov used four 'Progress D-27', designed by Ivchenko-Progress design Bureau, to power its mighty AN-70 transporters. It also planned on using a similar power plant for the wide-bodied AN-180 but the aircraft was never built.
On June 14, 2021, CFM International announced its RISE (Revolutionary Innovation for Sustainable Engines) program, which will look at developing a new Propfan to power the next generation of airliners.
CFM declared that the engine, with its "open-fan architecture," will be 20% more efficient than today's examples. It hopes to begin testing with a demonstrator by 2025, with a planned entry into service by the mid-2030s.
As oil prices once again reach record highs, we may once again see aircraft and engine manufacturers revisit the idea of the Unducted Fan engine.
Featured Image: McDonnell Douglas fitted both the GE36 and P&W 578-DX to an MD-80 demonstrator.
Find out more in our latest issue. Explore all the subscriptions plans that Airways has for you. From thrilling stories to insights into the commercial aviation industry. We are a global review of commercial flight.
Exploring Airline History Volume I
.webp)
David H. Stringer, the History Editor for AIRWAYS Magazine, has chronicled the story of the commercial aviation industry with his airline history articles that have appeared in AIRWAYS over two decades. Here, for the first time, is a compilation of those articles.
Subjects A through C are presented in this first of three volumes. Covering topics such as the airlines of Alaska at the time of statehood and Canada's regional airlines of the 1960s, the individual histories of such carriers as Allegheny, American, Braniff, and Continental are also included in Volume One. Get your copy today!