DALLAS — Imagine booking a flight and making it all the way to the gate, only to be told you can’t travel. Perhaps the bête noir of all imaginable travel experiences.
Yet, this is precisely what I witnessed las summer whilst traveling as a passenger. Before you jump to conclusions and assume that one too many passengers strayed towards the wrong gate, think again.
It was after arriving at the boarding gate where things began to unravel. As I inched closer in the queue, I witnessed several passengers being told they were denied boarding and would be accommodated on a later flight. What was initially a handful of disgruntled passengers continued to steadily swell in number.
Before relinquishing my boarding pass, I overheard gate staff declaring that only 105 passengers could travel. With this flight being operated by an Airbus A319 with over 150 seats, something seemed adrift.
Thankfully, I was one of the lucky passengers allowed to board, and I left London Gatwick Airport (LGW) as originally planned. My decision to check in early online proved particularly advantageous as the sole determining reason for me being granted a seat onboard.
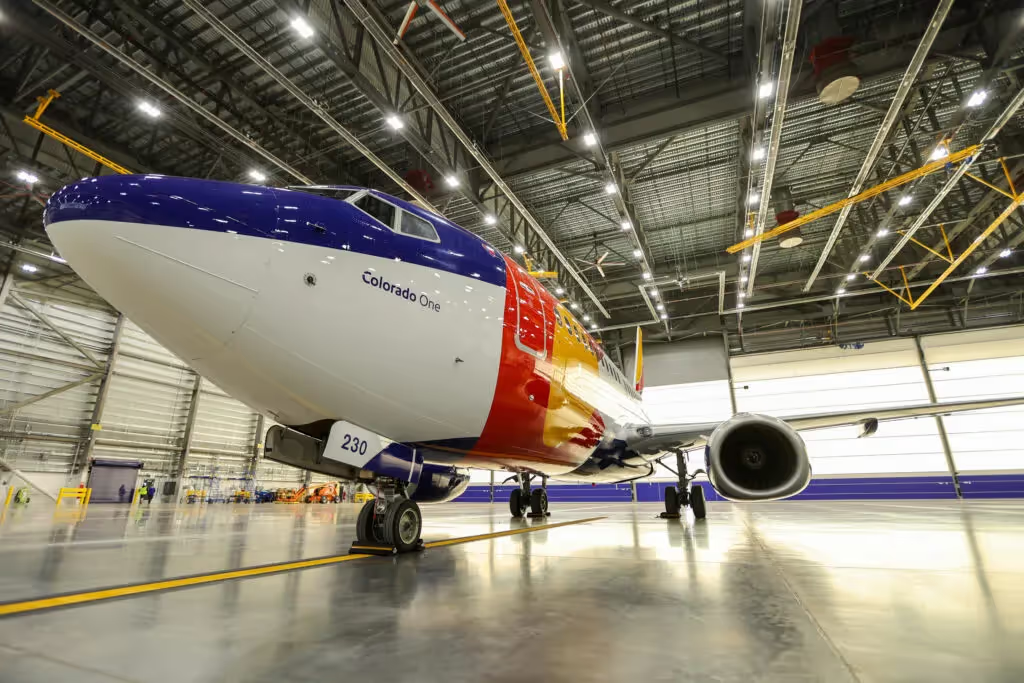
What Is the Minimum Equipment List?
Those less fortunate than myself had fallen foul of a document that few passengers will be aware of – the Minimum Equipment List (MEL). The MEL is a document that details what technical defects are permissible to be deferred for repair and which defects may infringe on the airworthiness of an aircraft.
In the latter case, such deficiencies must be repaired before the next departure. Contrary to what you may think, it is not uncommon for an aircraft to fly with at least one defect being deferred per the MEL.
Each aircraft type also has a Configuration Deviation List (CDL), which addresses external structural deficiencies. One example could be a missing lens cover that surrounds an external light, whereas the MEL would cover the operation of the light itself. The CDL is referred to far less frequently than the MEL.
During my recent trip, it transpired that the forward left cabin door could not be opened normally and was declared unserviceable. In this case, the MEL would have stated that the aircraft could be flown with an inoperative door, but the passenger capacity had to be limited.
One less serviceable door means one less emergency exit, which can be used in an emergency evacuation. This accounts for why the capacity was capped and why some of my fellow passengers were turned away from the gate.
The MEL also guides how long a defect can exist while permitting the aircraft to continue flying. The more complex the problem, the shorter the time concession the MEL affords. In the case of an unserviceable cabin door, repairs would likely be needed in a matter of days at the very most.
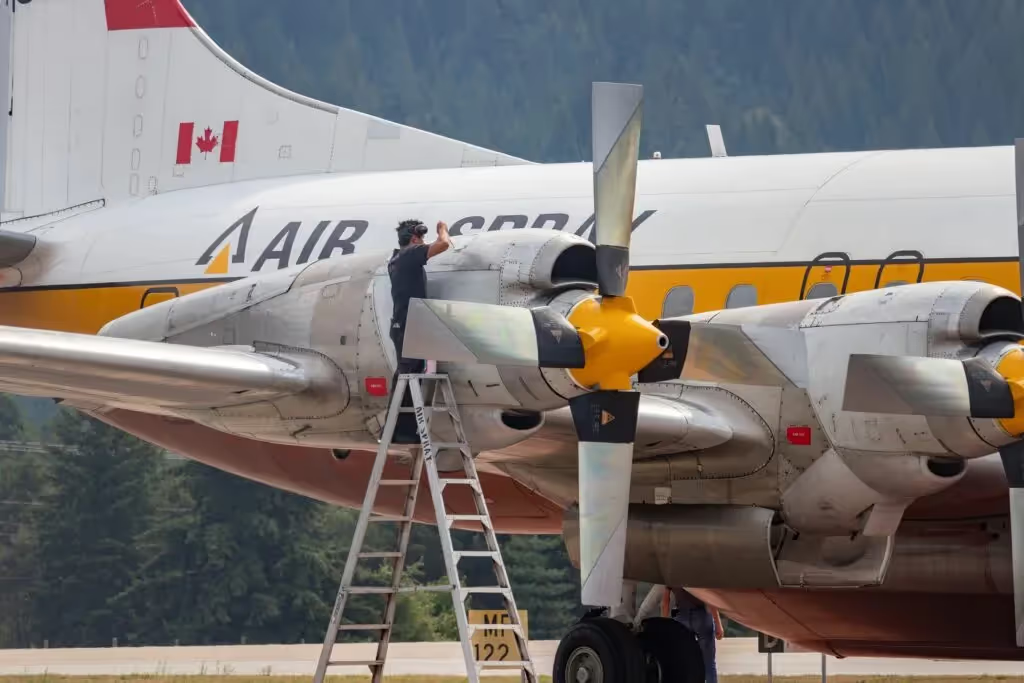
System Redundancy
Fortunately, modern aircraft are built with multiple layers of technical redundancy. For example, when a hydraulic system malfunctions, additional supporting systems will often still be able to absorb most, if not all, of the hydraulic demand placed on the inoperative system.
This abundance of redundancy, synonymous with modern aircraft, leads to ever-growing complexity. When part of a system malfunctions, rather than the entire system itself, how can it be determined if the optimum decision is to ground the aircraft and await repair?
With the adage of ‘aircraft only make money when they fly’, airlines are often limited by time when planning what defects can be repaired during a routine turnaround.
The situation is exacerbated to a greater degree for narrow-body aircraft, as they are often operated with shorter turnarounds than wide-body types. If every defect had to be fixed before the next journey, flight information displays within terminals would be awash with delays and cancellations.
But the shortage of time on the ground is not the only reason why the MEL gives airlines much-needed flexibility. This document also enables airlines to streamline the provision of engineering support.
If carriers had to maintain plentiful supplies of spare components at each destination they flew to, the logistical upheaval and overall costs would be immense. By eliminating the need to address every defect prior to each flight, the MEL gives airlines time to plan fleet scheduling. It enables aircraft to be rotated through maintenance hubs when needed.
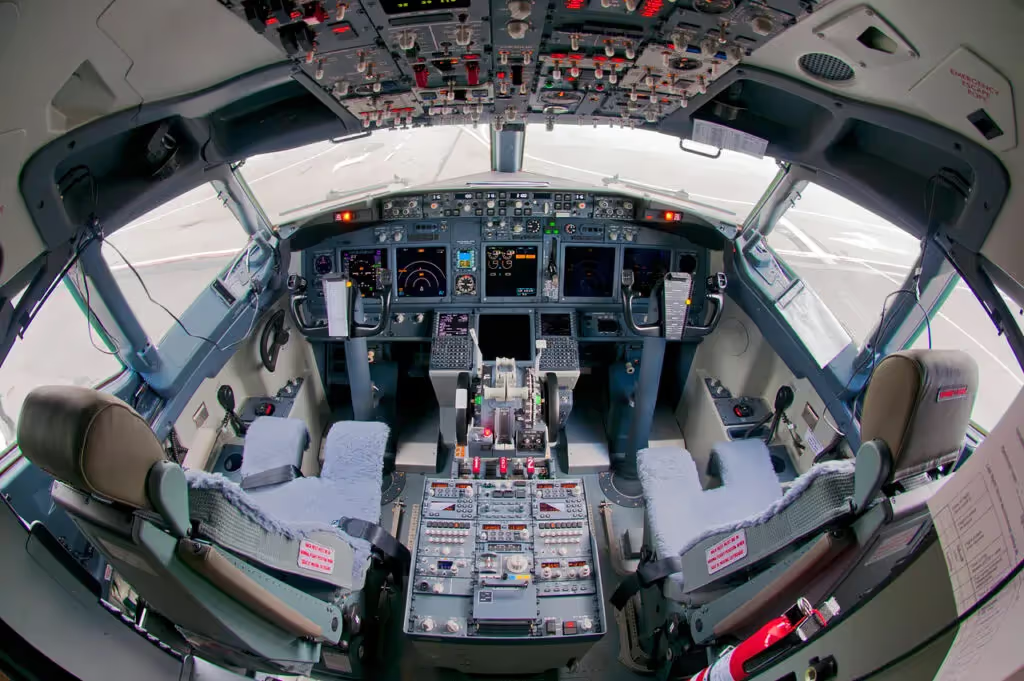
Manufacturer’s Guidance
Each airline is responsible for providing its own MEL document. Generally speaking, this will bear a substantial similarity to the Master Minimum Equipment List (MMEL), which the aircraft manufacturer drafts.
The expectation is that airlines should use the MMEL as a baseline to build their own procedures. While carriers have leeway to make their own MEL more restrictive than the MMEL and permit less flexibility, they cannot do the opposite and endorse a wider scope of technical irregularities.
Adherence to the MMEL applies not only to the nature of permitted defects but also to the length of time that can elapse before the discrepancy must be resolved.
With more trivial issues, airlines often have up to a few months to initiate repairs. Whilst the MMEL will address various technical defects, it will contain less rigid guidance covering what goes on inside the cabin.
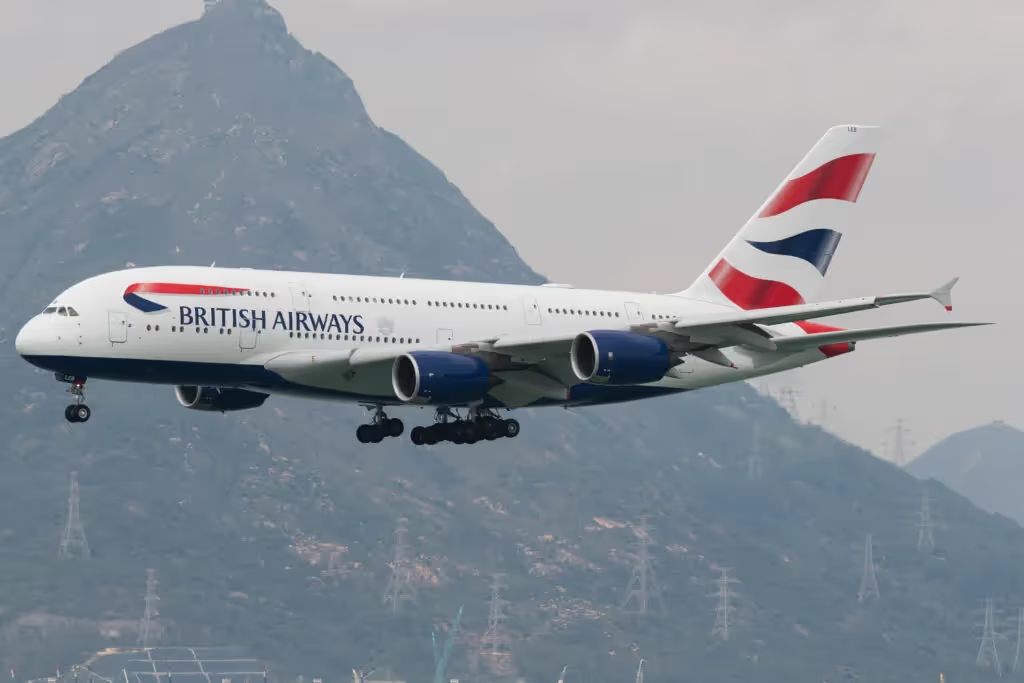
Cabin Differences
Interestingly, it is rare to see two exact copies of a MEL between airlines operating the same aircraft type. This is down to the differing cabin fixtures and fittings from one airline to the next.
To give context, an airline operating an Airbus A321 across the Atlantic will likely have more sophisticated cabin furnishings and emergency equipment than a carrier operating the same type only within a short-haul environment. Consequently, those plying longer routes will probably be bound by more lengthy MEL procedures.
For instance, a relatively benign defect, such as an inoperative seat-back entertainment screen, will be linked to a MEL provision. On the other hand, this will be absent from the MEL used by an airline that offers no inflight entertainment.
Another example can involve medical equipment carried on-board, which can vary widely from one airline to the next despite the same type being operated. Airlines often stipulate a minimum level of medical supplies and equipment that must be carried before departure.
Typically, used items will be replaced by engineers, but this may only sometimes be possible when replenishments are available at each destination. In such situations, the MEL will guide how much medical equipment must be carried before departure and when supplies must be restored.
.avif)
Quick Referencing
With the massive system redundancy that is commonplace with modern airliners nowadays, the MEL for any aircraft type is a large and cumbersome document.
To counteract this, manufacturers often use numerical indexing to aid quicker referencing. The first number or pair of numbers of a MEL reference usually denotes the system to which the MEL provision applies.
When the flight crew board an aircraft for their first flight of the day and study the aircraft’s Technical Log to verify the status of the airframe, any relevant MEL limitations will be scrutinised.
Engineers will record any applicable MEL limitations, which will be referenced as a unique index number. By using this numerical reference system, pilots can quickly and accurately locate the correct guidance within the document.
.avif)
Operational Limitations
When the MEL is used, pilots could be faced with something relatively minor and may simply have information to consider, as opposed to having to alter routine procedures when managing more complex defects.
For instance, an inoperative landing light is relatively minor and has few implications. Conversely, a partially operating electrical or hydraulic system could require far more thought and planning and could need the crew to add extra actions to their existing flow of procedures.
Having reduced electrical capability could lead to the necessity of keeping the Auxiliary Power Unit (APU) running during the flight. In turn, this would require a higher fuel burn to be accounted for.
So, not only does the MEL inform crews what inoperative items of equipment they can depart with, but the document also gives instructions on additional procedures that the manufacturer deems to be appropriate to maintain safety.
.avif)
MEL Applicability
It is worth pointing out that the regulations published in a MEL only apply whilst an aircraft is on the ground. The exact point when the MEL is no longer controlling can vary from airline to airline.
I have personally flown for one carrier, which stipulated that the closure of the last cabin door was when the MEL was no longer controlling. Alternatively, another airline mandated that the point of beginning to taxi to the runway was the transition point.
After the MEL is no longer controlling, it is commonplace for crews to refer to the abnormal checklist should they be presented with a technical malfunction requiring pilot intervention. Nonetheless, the MEL can often provide meaningful insight into a technical discrepancy that may arise, even if the guidance in the document is no longer applicable.
One particular use for the MEL in the air is to ascertain the operational impact that a specific defect or defects may have on the next flight. Imagine a technical issue develops in the air, and the pilots determine that the MEL allows no flexibility to depart with this hypothetical unserviceability.
In such situations, an intended destination with limited technical support may no longer be the optimum destination. To the chagrin of the passengers on board, an en-route diversion to an airport with sufficient technical support may be the preferable solution.
The MEL is a means to balance economic efficiency against maintaining an acceptable level of safety. Whilst flight crews will be well versed in their routine procedures, the MEL is an additional document that all pilots become very familiar with, especially when flying more elderly aircraft types.
While, in my case, the MEL resulted in passengers being offloaded, it ultimately enables airlines to maintain schedule efficiency and get passengers and cargo to their destination as planned, rather than having to cancel flights and disrupt the plans of many travellers.